Manufacturing process of graphene transparent conductive film
A transparent conductive film, graphene film technology, applied in cable/conductor manufacturing, circuits, electrical components, etc., can solve the problems of conductive film conductivity decline, inability to meet performance requirements, affecting graphene conductivity, etc., to achieve film formation Short time, low cost, clear pattern effect
- Summary
- Abstract
- Description
- Claims
- Application Information
AI Technical Summary
Problems solved by technology
Method used
Examples
Embodiment Construction
[0030] In order to make the technical means, creative features, goals and effects achieved by the present invention easy to understand, the present invention will be further described below in conjunction with specific embodiments.
[0031] A method for preparing a patterned graphene conductive film according to the present implementation, the graphene conductive film includes a graphene layer and a film as a substrate, the thickness of the copper foil is 20-50 μm, and the purity is more than 99.9%. The film is polyethylene terephthalate (PET), polycarbonate (PC) or polymethylmethacrylate (PMMA); its thickness is 150~200μm, the thickness tolerance is less than ±2μm, and the light transmittance is greater than 93 %, the haze is less than 1%; the thickness of the copper foil in this example is 30 μm, the purity is 99.99%, the thickness of the film is 180 μm, the thickness tolerance is less than ±1 μm, and the light transmittance is 96%. On the surface of the film There is also a ha
PUM
Property | Measurement | Unit |
---|---|---|
Thickness | aaaaa | aaaaa |
Thickness | aaaaa | aaaaa |
Thickness | aaaaa | aaaaa |
Abstract
Description
Claims
Application Information
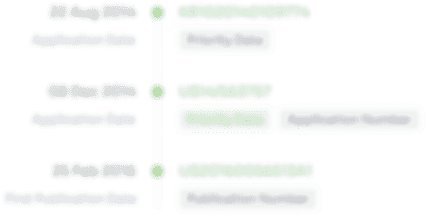
- R&D Engineer
- R&D Manager
- IP Professional
- Industry Leading Data Capabilities
- Powerful AI technology
- Patent DNA Extraction
Browse by: Latest US Patents, China's latest patents, Technical Efficacy Thesaurus, Application Domain, Technology Topic.
© 2024 PatSnap. All rights reserved.Legal|Privacy policy|Modern Slavery Act Transparency Statement|Sitemap