Die-casting method of thin-wall oil pipe embedding part oil pan
一种油底壳、油管的技术,应用在转子、汽缸、定子等方向,能够解决油管没有放到位、油管易压扁变形、油管定位孔跑铝等问题,达到定位准确的效果
- Summary
- Abstract
- Description
- Claims
- Application Information
AI Technical Summary
Problems solved by technology
Method used
Examples
Embodiment 1
[0023] Example 1: put the oil pipe into the oven to preheat, put the No. 1 oil pipe 1 on the upper layer of the oven, and put the No. 2 oil pipe 2 on the lower layer. The time is 5 minutes; after the production is completed, the operator clamps the sprue of the oil pan with pliers, drags the bottom of the oil pan 8 with a wooden hammer, and puts the product on the knocking platform, and the operator holds the sprue of the product with the pliers in his left hand , take a wooden hammer in the right hand to remove the slag bag of the product, and then use the wooden hammer to break off the runners on both sides. The wooden hammer hits the middle of the material handle to break the material handle. pieces, put six layers, 36 pieces per board.
Embodiment 2
[0024] Example 2: put the oil pipe into the oven to preheat, put No. 1 oil pipe 1 on the upper layer of the oven, and No. 2 oil pipe 2 on the lower layer. The time is 5 minutes; after the production is completed, the operator clamps the sprue of the oil pan with pliers, drags the bottom of the oil pan 8 with a wooden hammer, and puts the product on the knocking platform, and the operator holds the sprue of the product with the pliers in his left hand , take a wooden hammer in the right hand to remove the slag bag of the product, and then use the wooden hammer to break off the runners on both sides. The wooden hammer hits the middle of the material handle to break the material handle. pieces, put six layers, 36 pieces per board.
Embodiment 3
[0025] Example 3: put the oil pipe into the oven to preheat, put No. 1 oil pipe 1 in the upper layer of the oven, and put No. 2 oil pipe 2 in the lower layer. The time is 5 minutes; after the production is completed, the operator clamps the sprue of the oil pan with pliers, drags the bottom of the oil pan 8 with a wooden hammer, puts the product on the knocking nozzle table, and the operator holds the sprue of the product with the pliers in his left hand , take a wooden hammer in the right hand to remove the slag bag of the product, and then use the wooden hammer to break off the runners on both sides. The wooden hammer hits the middle of the material handle to break the material handle. pieces, put six layers, 36 pieces per board.
[0026] To sum up, the present invention has the following advantages: the oil pipe is positioned accurately, the positioning hole of the oil pipe will not leak aluminum, and the oil pipe will not be flattened and deformed due to uneven force.
PUM
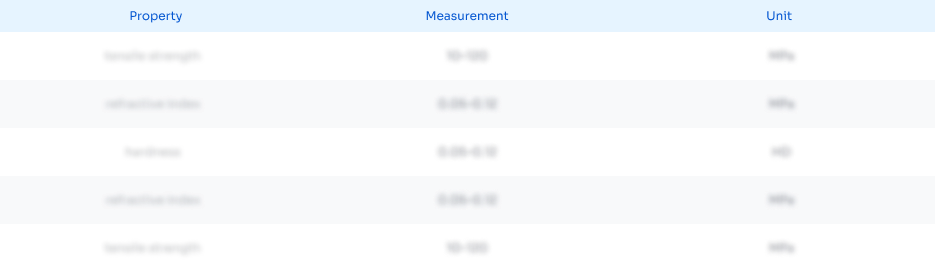
Abstract
Description
Claims
Application Information
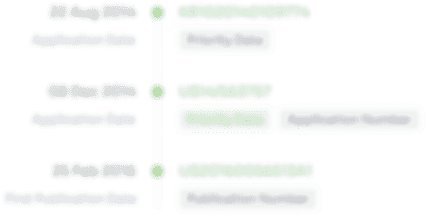
- R&D Engineer
- R&D Manager
- IP Professional
- Industry Leading Data Capabilities
- Powerful AI technology
- Patent DNA Extraction
Browse by: Latest US Patents, China's latest patents, Technical Efficacy Thesaurus, Application Domain, Technology Topic.
© 2024 PatSnap. All rights reserved.Legal|Privacy policy|Modern Slavery Act Transparency Statement|Sitemap