Wire-submerged brazing processing method of heat exchanger for large automobile
A heat exchanger and processing method technology, applied in heat exchange equipment, metal processing, metal processing equipment and other directions, can solve the problems of high production cost, idle difficulty, etc., achieve low equipment requirements, improve production efficiency, and simple processing. Effect
- Summary
- Abstract
- Description
- Claims
- Application Information
AI Technical Summary
Problems solved by technology
Method used
Examples
Example Embodiment
[0013] The buried wire brazing processing method of the heat exchanger for a large automobile of the present invention includes the following steps:
[0014] In the first step, the weldment is processed. The tube sheet and the end are welded by dissimilar materials. Due to the large matching size, in order to ensure the sealing and pressure requirements of the weldment, a copper alloy welding wire gas welding method is used in advance to weld the tube sheet and the end. Together, and then process the hole on the tube plate. On the milling machine, use the universal indexing head and the spindle hanging wheel method to perform straight-line shifting to process the drill mold. On the ordinary drilling machine, use the composite drill and When the guide reamer is clamped between the drill mold and the tube sheet, a rolling clamp is used to reduce the friction coefficient between the clamp and the working surface of the drill press;
[0015] The second step is to place the weldment. The a
PUM
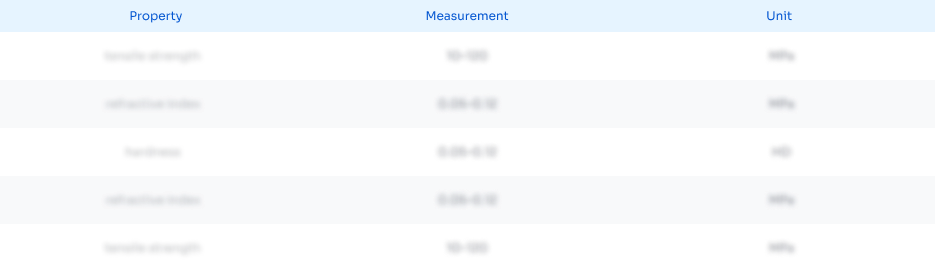
Abstract
Description
Claims
Application Information
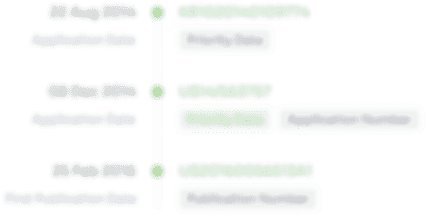
- R&D Engineer
- R&D Manager
- IP Professional
- Industry Leading Data Capabilities
- Powerful AI technology
- Patent DNA Extraction
Browse by: Latest US Patents, China's latest patents, Technical Efficacy Thesaurus, Application Domain, Technology Topic.
© 2024 PatSnap. All rights reserved.Legal|Privacy policy|Modern Slavery Act Transparency Statement|Sitemap