Production method of conductive pure-cotton fabric
A fabric and pure cotton technology, applied in textiles and papermaking, fiber treatment, physical treatment, etc., can solve the problem of affecting fabric softness and wearing comfort, affecting fabric conductivity, antistatic performance, weakening fabric conductivity, antistatic performance, etc. problem, to achieve the effect of controllable arrangement, overcoming comfort and soft hand feeling
- Summary
- Abstract
- Description
- Claims
- Application Information
AI Technical Summary
Problems solved by technology
Method used
Image
Examples
Embodiment 1
[0076] A preparation method of conductive pure cotton fabric, comprising the following steps:
[0077] (1) Preparation of photo-induced free radical polymer composite finishing solution:
[0078] Each 1 liter of photo-induced radical polymer composite finishing solution is composed of the following components: 2.5 g of sulfonated polyether ether ketone with a degree of etherification of 70%; 5 g of hydrogen atom donor polymer; 1 wt% of cross-linking agent (cross-linking agent The weight of the sulfonated polyether ether ketone and the percentage of the total weight of the hydrogen atom donor polymer); an appropriate amount of acetic acid adjusts the pH value of the finishing solution to 5; the balance is deionized water, and the solution is made into 1 liter; hydrogen atom donor polymerization The substance is polyvinyl alcohol, and the cross-linking agent is glutaraldehyde;
[0079] Preparation steps: put the sulfonated polyether ether ketone and 400 mL of deionized water in...
Embodiment 2
[0087] A preparation method of conductive pure cotton fabric, comprising the following steps:
[0088] (1) Preparation of photo-induced free radical polymer composite finishing solution:
[0089] Each 1 liter of photo-induced radical polymer composite finishing solution is composed of the following components: 4.7 g of sulfonated polyether ether ketone with a degree of etherification of 73.8%; 7.4 g of hydrogen atom donor polymer; 3.8 wt% of crosslinking agent (crosslinking agent) The weight of the linking agent accounts for the percentage of the total weight of the sulfonated polyether ether ketone and the hydrogen atom donor polymer); an appropriate amount of acetic acid adjusts the pH value of the finishing solution to 4; the balance is deionized water, and the solution is made into 1 liter; hydrogen atom donor The bulk polymer is polyethyleneimine, and the cross-linking agent is epichlorohydrin;
[0090] Preparation steps: put the sulfonated polyether ether ketone and 500...
Embodiment 3
[0098] A preparation method of conductive pure cotton fabric, comprising the following steps:
[0099] (1) Preparation of photo-induced free radical polymer composite finishing solution:
[0100] Each 1 liter of photo-induced radical polymer composite finishing solution is composed of the following components: 7.3 g of sulfonated polyether ether ketone with a degree of etherification of 81.2%; 10.9 g of hydrogen atom donor polymer; The weight of the sulfonated polyether ether ketone and the hydrogen atom donor polymer is the percentage of the total weight of the sulfonated polyether ether ketone and the hydrogen atom donor polymer); an appropriate amount of acetic acid adjusts the pH value of the finishing solution to 3.4; the balance is deionized water, and the solution is made into 1 liter; the hydrogen atom donor The polymer is polyethyleneimine, and the cross-linking agent is epichlorohydrin;
[0101] Preparation steps: put the sulfonated polyether ether ketone and 400 mL...
PUM
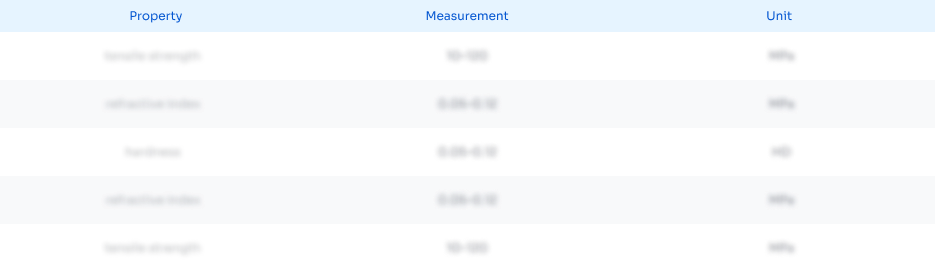
Abstract
Description
Claims
Application Information
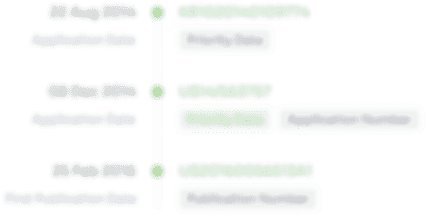
- R&D Engineer
- R&D Manager
- IP Professional
- Industry Leading Data Capabilities
- Powerful AI technology
- Patent DNA Extraction
Browse by: Latest US Patents, China's latest patents, Technical Efficacy Thesaurus, Application Domain, Technology Topic.
© 2024 PatSnap. All rights reserved.Legal|Privacy policy|Modern Slavery Act Transparency Statement|Sitemap