Method for dyeing carboxymethyl chitosan silicon-modified cotton fabric with natural dyes
A technology of carboxymethyl chitosan silicon and carboxymethyl chitosan is applied in the field of natural dye dyeing of carboxymethyl chitosan silicon modified cotton fabrics, and can solve the problems of low affinity, dye uptake and color fastness. Not high problems, to achieve the effect of good affinity, improved color fastness to soaping, and reduced dyeing temperature
- Summary
- Abstract
- Description
- Claims
- Application Information
AI Technical Summary
Benefits of technology
Problems solved by technology
Method used
Examples
Embodiment 1
[0025] 1) Take 20g of chitin, soak it in 60% sodium hydroxide solution at 60°C for 8 hours, wash it with hot water until neutral, dry it at 60°C, grind it finely to obtain chitosan;
[0026] 2) Dissolve chitosan in dilute acetic acid, precipitate with excess acetone to obtain chitosan acetate, transfer it to a stirred reaction vessel, add NaOH solution and isopropanol, and add chlorine dropwise while stirring The isopropanol solution of acetic acid is controlled at a reaction temperature of 65° C., reacted for 4 hours, cooled to room temperature, adjusted to neutral pH with dilute acid, washed with 85 wt % methanol, and dried to obtain carboxymethyl chitosan;
[0027] 3) Use 6g / L carboxymethyl chitosan solution, add 5mL glycidyl trimethoxysiloxane, and stir until it is completely dissolved under the condition that the bath ratio is 1:200 and the pH value is adjusted to 8 with ammonia water Carboxymethyl chitosan silicon hybrid system can be obtained;
[0028] 4) Treat the cott
Embodiment 2
[0034] 1) Take 30g of chitin, soak it in 60% sodium hydroxide solution at 60°C for 12h, wash it with hot water until neutral, dry it at 60°C, grind it finely to get chitosan;
[0035] 2) Dissolve chitosan in dilute acetic acid, precipitate with excess acetone to obtain chitosan acetate, transfer it to a stirred reaction vessel, add NaOH solution and isopropanol, and add chlorine dropwise while stirring The isopropanol solution of acetic acid is controlled at a reaction temperature of 65° C., reacted for 4 hours, cooled to room temperature, adjusted to neutral pH with dilute acid, washed with 85 wt % methanol, and dried to obtain carboxymethyl chitosan;
[0036] 3) Use 9g / L carboxymethyl chitosan solution, add 7.5mL glycidyltrimethoxysiloxane, and stir until all Carboxymethyl chitosan silicon hybrid system can be obtained by dissolving;
[0037] 4) Treat the cotton fabric with the above solution in a constant temperature oscillating dyeing machine at 40°C. After treatment for 9
Embodiment 3
[0043] 1) Take 10g of chitin, soak it in 60% sodium hydroxide solution at 60°C for 4 hours, wash it with hot water until it becomes neutral, dry it at 60°C, and grind it finely to obtain chitosan;
[0044]2) Dissolve chitosan in dilute acetic acid, precipitate with excess acetone to obtain chitosan acetate, transfer it to a stirred reaction vessel, add NaOH solution and isopropanol, and add chlorine dropwise while stirring The isopropanol solution of acetic acid is controlled at a reaction temperature of 65° C., reacted for 4 hours, cooled to room temperature, adjusted to neutral pH with dilute acid, washed with 85 wt % methanol, and dried to obtain carboxymethyl chitosan;
[0045] 3) Use 3g / L carboxymethyl chitosan solution, add 2.5mL glycidyltrimethoxysiloxane, and stir until all Carboxymethyl chitosan silicon hybrid system can be obtained by dissolving;
[0046] 4) Treat the cotton fabric with the above solution at 40°C in a constant temperature oscillating dyeing machine.
PUM
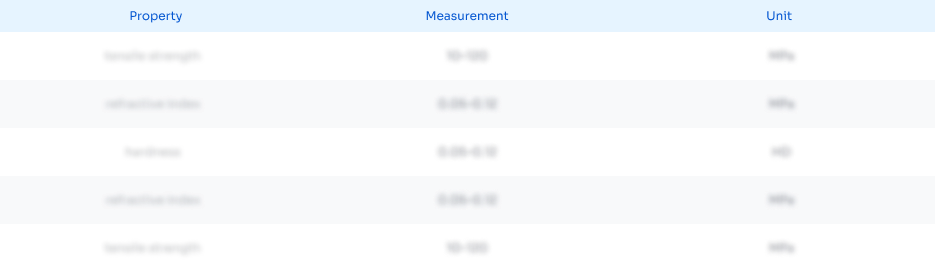
Abstract
Description
Claims
Application Information
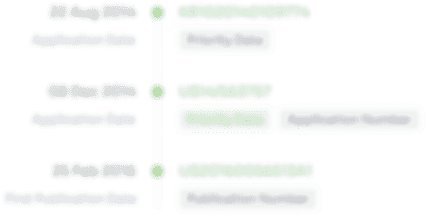
- R&D Engineer
- R&D Manager
- IP Professional
- Industry Leading Data Capabilities
- Powerful AI technology
- Patent DNA Extraction
Browse by: Latest US Patents, China's latest patents, Technical Efficacy Thesaurus, Application Domain, Technology Topic.
© 2024 PatSnap. All rights reserved.Legal|Privacy policy|Modern Slavery Act Transparency Statement|Sitemap