Method for preparing high-density fused magnesite by reburning electric smelting composite process
A composite process, the technology of fused magnesia, which is applied in the field of fused magnesia smelting, can solve the problems of low density of fused magnesia, and achieve the effects of reducing porosity, increasing density, and remarkable exhaust effect
- Summary
- Abstract
- Description
- Claims
- Application Information
AI Technical Summary
Problems solved by technology
Method used
Image
Examples
Example Embodiment
[0018] Example 1
[0019] Calcined 10 kg of magnesite ore with a mass percentage of 45% by mass in a high temperature shaft kiln at 1450°C for 4 hours to obtain recalcined magnesia; crush the recalcined magnesia in a jaw crusher to a particle size of 60- 80mm block; melt the block with a particle size of 60-80mm in an electric arc furnace at 2650℃ (the diameter of the graphite electrode of the arc furnace is 300mm, the bending strength of the graphite electrode is 10MPa, the compressive strength of the graphite electrode is 20MPa, and the ash content of the graphite electrode is 0.5 %), the submerged arc melting time is 10h; the molten fused magnesia lumps are naturally cooled for 7 days; the cooled fused magnesia lumps are manually broken to obtain the molten fused magnesia lumps.
[0020] According to GB / T2997-2000, the volume density and porosity of the test sample are measured; the crystal grain size of the sample is measured under the Zeiss-ΣIGMA-HD scanning electron microscope
Example Embodiment
[0021] Example 2
[0022] Calcined 10kg of magnesite ore with a mass percentage of 46% magnesia in a high temperature shaft kiln at 1500°C for 4 hours to obtain recalcined magnesia; crush the recalcined magnesia in a jaw crusher to a particle size of 70- 90mm block material; melt the block material with a particle size of 70-90mm in an electric arc furnace at 2750℃ (the diameter of the graphite electrode of the arc furnace is 300mm, the bending strength of the graphite electrode is 10MPa, the compressive strength of the graphite electrode is 20MPa, and the ash content of the graphite electrode is 0.5 %), the submerged arc melting time is 10h; the molten fused magnesia lumps are naturally cooled for 8 days; the cooled fused magnesia lumps are broken manually to obtain the molten fused magnesia lumps.
[0023] According to GB / T2997-2000, the volume density and porosity of the test sample are measured; the crystal grain size of the sample is measured under the Zeiss-ΣIGMA-HD scanning e
Example Embodiment
[0024] Example 3
[0025] Calcined 10kg of magnesite ore with a mass percentage of 47% magnesia in a high temperature shaft kiln at 1600°C for 4 hours to obtain recalcined magnesia; crush the recalcined magnesia in a cone crusher to produce a particle size of 80-100mm The block material with a particle size of 80-100mm is melted in an electric arc furnace at 2750℃ (the diameter of the graphite electrode of the arc furnace is 300mm, the bending strength of the graphite electrode is 10MPa, the compressive strength of the graphite electrode is 20MPa, and the ash content of the graphite electrode is 0.5% ), the submerged arc melting time is 10h; the molten fused magnesia lumps are naturally cooled for 8 days; the cooled fused magnesia lumps are manually broken to obtain the molten fused magnesia lumps.
[0026] According to GB / T2997-2000, the volume density and porosity of the test sample are measured; the crystal grain size of the sample is measured under the Zeiss-ΣIGMA-HD scanning el
PUM
Property | Measurement | Unit |
---|---|---|
Diameter | aaaaa | aaaaa |
Flexural strength | aaaaa | aaaaa |
Compressive strength | aaaaa | aaaaa |
Abstract
Description
Claims
Application Information
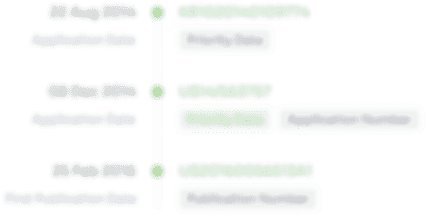
- R&D Engineer
- R&D Manager
- IP Professional
- Industry Leading Data Capabilities
- Powerful AI technology
- Patent DNA Extraction
Browse by: Latest US Patents, China's latest patents, Technical Efficacy Thesaurus, Application Domain, Technology Topic.
© 2024 PatSnap. All rights reserved.Legal|Privacy policy|Modern Slavery Act Transparency Statement|Sitemap