Photocurable polyester oligomer for 3D printing as well as preparation method and application thereof
A polyester oligomer and 3D printing technology, applied in the field of biomedical materials, can solve the problems of low printing efficiency and achieve the effect of excellent performance, broad application prospects and low viscosity
- Summary
- Abstract
- Description
- Claims
- Application Information
AI Technical Summary
Problems solved by technology
Method used
Image
Examples
Embodiment 1
[0030] (1) Preparation of photocurable polylactic acid PLA oligomer: Add 68g of L-lactic acid solution into a three-necked flask, gradually raise the temperature to 90°C under 20KPa, stir and dehydrate for 2 hours, then add 13.71g of 1,6 hexanedi Alcohol and 0.21g catalyst stannous octoate, continue to react at 10kPa, 130°C for 2h, then dehydrate at 1000Pa, 150°C for 1h, cool to 100°C under vacuum, add 0.4g polymerization inhibitor p-hydroxyanisole and 40g methacrylic acid Anhydride, and then heated to 120 ° C under normal pressure for 4 hours, heated to 140 ° C under reduced pressure to extract excess methacrylic anhydride, cooled to room temperature to obtain polylactic acid oligomers. Add 40g of tetrahydrofuran to the obtained product, stir and dissolve, then slowly add to a separatory funnel containing 400g of n-hexane, shake it several times and let it stand for a period of time, take out the lower layer of liquid; repeat three times; then put the lower layer of liquid into t
Embodiment 2
[0033](1) Preparation of photocurable polycaprolactone PCL oligomer: Add 86g of L-lactic acid solution into a three-necked flask, gradually raise the temperature to 90°C at 20KPa, stir and dehydrate for 2 hours, then add 13g of 1,2- Butanediol and 0.2g catalyst stannous octoate, continue to react at 10KPa, 130°C for 2h, then dehydrate at 1000Pa, 150°C for 1h, cool to 100°C under vacuum, add 0.4g polymerization inhibitor 2,6-di-tert-butyl p-cresol and 40g of methacrylic anhydride were heated to 120°C for 4 hours under normal pressure, and the excess methacrylic anhydride was extracted under reduced pressure at 140°C, and cooled to room temperature to obtain polylactic acid oligomers. Add 50g of tetrahydrofuran to the obtained product, stir and dissolve it, then slowly add it into a separatory funnel containing 500g of n-hexane, shake it several times and let it stand for a while, take out the lower layer of liquid; repeat three times; then put the lower layer of liquid into the dia
Embodiment 3
[0036] (1) Preparation of photocurable polylactic acid PLA oligomer: Add 68g of L-lactic acid solution into a three-necked flask, gradually raise the temperature to 90°C under 20KPa, stir and dehydrate for 2h, then add 10g of glycerin and 0.21g of catalyst Stannous chloride, continue to react at 10KPa, 130°C for 2h, then dehydrate at 1000Pa, 150°C for 1h, cool to 100°C under vacuum, add 0.4g of polymerization inhibitor p-hydroxyanisole and 40g of methacrylic anhydride, and then Raise the temperature to 120°C for 4 hours under normal pressure, raise the temperature to 140°C to extract excess methacrylic anhydride under reduced pressure, and cool to room temperature to obtain a star-shaped polylactic acid oligomer. Add 40g of tetrahydrofuran to the obtained product, stir and dissolve, then slowly add to a separatory funnel containing 400g of n-hexane, shake it several times and let it stand for a period of time, take out the lower layer of liquid; repeat three times; then put the lo
PUM
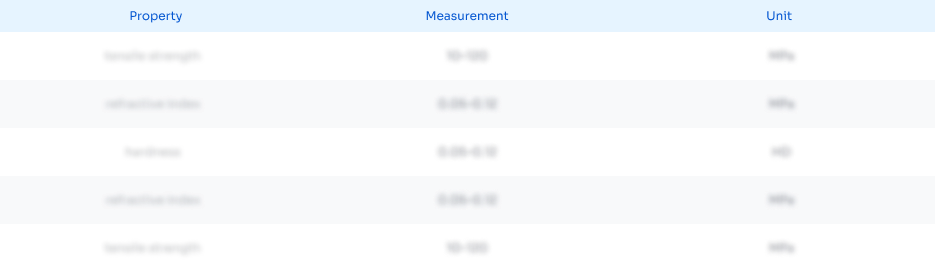
Abstract
Description
Claims
Application Information
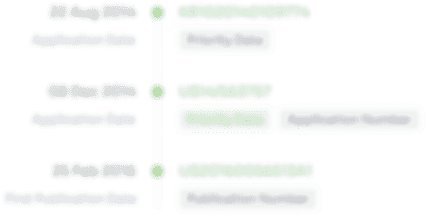
- R&D Engineer
- R&D Manager
- IP Professional
- Industry Leading Data Capabilities
- Powerful AI technology
- Patent DNA Extraction
Browse by: Latest US Patents, China's latest patents, Technical Efficacy Thesaurus, Application Domain, Technology Topic.
© 2024 PatSnap. All rights reserved.Legal|Privacy policy|Modern Slavery Act Transparency Statement|Sitemap