Ordered mesoporous silica-glass fiber paper composite material as well as preparation method and application thereof
A technology of glass fiber paper and composite materials, applied in the direction of silicon compounds, separation methods, chemical instruments and methods, etc., can solve the problems of active component sintering, high coating requirements, small specific surface area, etc., and achieve a high degree of order , simple process, large specific surface area
- Summary
- Abstract
- Description
- Claims
- Application Information
AI Technical Summary
Problems solved by technology
Method used
Image
Examples
Embodiment 1
[0032] A method for preparing an ordered mesoporous silicon-glass fiber paper composite material provided in this embodiment comprises the following steps:
[0033] (1) Soak 50g of silicon powder in hot water for 10 minutes to activate it. When it is thin paste, add it to a three-necked flask filled with 0.5mol / L NaOH solution, stir and heat. The reaction temperature is 90°C, and the reaction time is 8h, obtain nano-silica sol;
[0034] (2) The sodium silicate of 5g is dissolved in the deionized water of 15g, the polyethylene oxide-polyoxypropylene-polyoxyethylene triblock copolymer (P123) of 2g is dissolved in 70mL mass fraction is In 15% hydrochloric acid aqueous solution, mix the above two solutions;
[0035] (3) Pour the mixed solution obtained in step (2) into a hydrothermal reaction kettle for hydrothermal reaction. The reaction conditions are 35°C hydrothermal for 24 hours, 100°C hydrothermal for 24h; then filter, wash, dry, and finally in the muffle Calcined in a furn
Embodiment 2
[0041] A method for preparing an ordered mesoporous silicon-glass fiber paper composite material provided in this embodiment comprises the following steps:
[0042] (1) Soak 50g of silicon powder in hot water for 10 minutes to activate it. When it is thin paste, add it to a three-necked flask filled with 0.5mol / L NaOH solution, stir and heat. The reaction temperature is 90°C, and the reaction time is 8h, obtain nano-silica sol;
[0043] (2) The sodium silicate of 5g is dissolved in the deionized water of 15g, the polyethylene oxide-polyoxypropylene-polyoxyethylene triblock copolymer (P123) of 2g is dissolved in 70mL mass fraction is In 15% hydrochloric acid aqueous solution, mix the above two solutions;
[0044] (3) Pour the mixed solution obtained in step (2) into a hydrothermal reaction kettle for hydrothermal reaction. The reaction conditions are 35°C hydrothermal for 24 hours, 100°C hydrothermal for 24h; then filter, wash, dry, and finally in the muffle Calcined in a furn
Embodiment 3
[0050] A method for preparing an ordered mesoporous silicon-glass fiber paper composite material provided in this embodiment comprises the following steps:
[0051] (1) Soak 50g of silicon powder in hot water for 10 minutes to activate it. When it is thin paste, add it to a three-necked flask filled with 0.5mol / L NaOH solution, stir and heat. The reaction temperature is 90°C, and the reaction time is 8h, obtain nano-silica sol;
[0052] (2) The sodium silicate of 5g is dissolved in the deionized water of 15g, the polyethylene oxide-polyoxypropylene-polyoxyethylene triblock copolymer (P123) of 2g is dissolved in 70mL mass fraction is In 15% hydrochloric acid aqueous solution, mix the above two solutions;
[0053] (3) Pour the mixed solution obtained in step (2) into a hydrothermal reaction kettle for hydrothermal reaction. The reaction conditions are 35°C hydrothermal for 24 hours, 100°C hydrothermal for 24h; then filter, wash, dry, and finally in the muffle Calcined in a furn
PUM
Property | Measurement | Unit |
---|---|---|
The average particle size | aaaaa | aaaaa |
Abstract
Description
Claims
Application Information
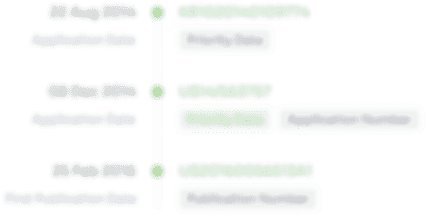
- R&D Engineer
- R&D Manager
- IP Professional
- Industry Leading Data Capabilities
- Powerful AI technology
- Patent DNA Extraction
Browse by: Latest US Patents, China's latest patents, Technical Efficacy Thesaurus, Application Domain, Technology Topic.
© 2024 PatSnap. All rights reserved.Legal|Privacy policy|Modern Slavery Act Transparency Statement|Sitemap