Lightweight cylinder sleeve and preparation process thereof
A preparation process and cylinder liner technology, applied in the direction of manufacturing tools, cylinders, cylinder heads, etc., can solve the problems of reducing the volume and weight of the engine, the volume and weight of the cylinder liner, and the preparation method is not set, so as to reduce the quality and accelerate the solidification Speed, cost reduction effects
- Summary
- Abstract
- Description
- Claims
- Application Information
AI Technical Summary
Problems solved by technology
Method used
Examples
Example Embodiment
[0036] Example 1
[0037] see Figure 1-2 As shown, a lightweight cylinder liner includes a cylinder block 1, and several pits 2 are arranged on one side of the annular outer surface of the cylinder block 1, and the top of the pits 2 is an arc surface, and the annular outer surface of the cylinder block 1 has a There is a transmission shaft fixing hole 3 on the side;
[0038] The preparation process of the cylinder liner comprises the following steps:
[0039] Step S1, smelting casting fluid: Melting the following components in the melting furnace in weight percentage: C3.0, SI2.0, Mn0.4, P0.15, S0.06, Cr0.2, Mo0.3, Ni0 .4, bainite 1.19, ferrite 0.05, and the rest are pearlite;
[0040] Step S2, preparation of coating liquid: in parts by weight, take 3 parts of bentonite, 5 parts of diatomite, 25 parts of water, and 1 part of titanium alloy powder, add bentonite to water and stir in advance, control the speed and duration of the stirring device, and then Add diatomaceous eart
Example Embodiment
[0051] Example 2
[0052] see Figure 1-2 As shown, a lightweight cylinder liner includes a cylinder block 1, and several pits 2 are arranged on one side of the annular outer surface of the cylinder block 1, and the top of the pits 2 is an arc surface, and the annular outer surface of the cylinder block 1 has a There is a transmission shaft fixing hole 3 on the side;
[0053] The preparation process of the cylinder liner comprises the following steps:
[0054] Step S1, smelting casting fluid: Melting the following components in the melting furnace in weight percentage: C3.4, SI2.7, Mn0.7, P0.1, S0.02, Cr0.4, Mo0.6, Ni0 .8, 3.54 bainite, 0.02 ferrite, and the rest are pearlite;
[0055] Step S2, preparation of coating liquid: in parts by weight, take 11 parts of bentonite, 50 parts of diatomite, 90 parts of water, and 3 parts of titanium alloy powder, add bentonite to water and stir in advance, control the speed and duration of the stirring device, and then Add diatomaceous ea
Example Embodiment
[0073] Example 3
[0074] see Figure 3-5 As shown, the centrifuge 4 for centrifugation includes a bottom plate 41, the upper end of the bottom plate 41 is fixedly equipped with a working drum 42, the inner output end of the working drum 42 is fixedly installed with a connecting cylinder 421, and a hollow cylinder 421 is provided inside the connecting cylinder 421. Circular groove 422, a plurality of clamping grooves 423 are provided at the positions around the inner wall of the hollow circular groove 422, and a rotating screw 424 is connected to the surrounding positions of the circular outer surface of the connecting cylinder 421 for rotation;
[0075] An embedded block 44 is clamped inside the card slot 423, and a built-in through slot 441 is opened inside the embedded block 44, and a movable flip cover 43 is movably connected to the upper end of the connecting cylinder 421;
[0076] Before placing the external mold inside the hollow circular groove 422, insert the embedded b
PUM
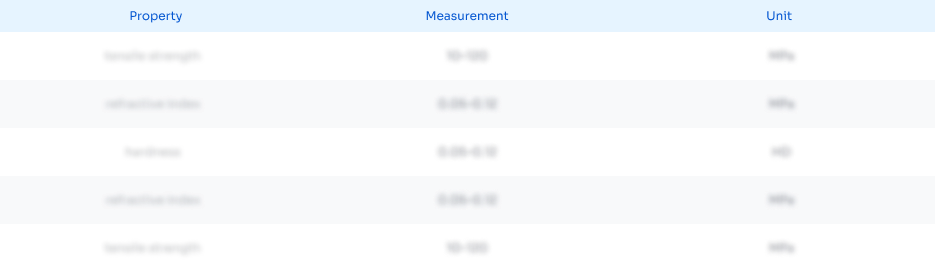
Abstract
Description
Claims
Application Information
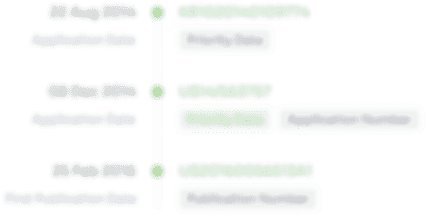
- R&D Engineer
- R&D Manager
- IP Professional
- Industry Leading Data Capabilities
- Powerful AI technology
- Patent DNA Extraction
Browse by: Latest US Patents, China's latest patents, Technical Efficacy Thesaurus, Application Domain, Technology Topic.
© 2024 PatSnap. All rights reserved.Legal|Privacy policy|Modern Slavery Act Transparency Statement|Sitemap