Continuous spheroidizing annealing method for high-carbon chromium bearing steel round steel
A technology of high carbon chromium bearing steel and continuous annealing furnace, which is applied in the field of heat treatment of steel materials, can solve the problems of uneven spheroidized structure, long annealing process time, poor treatment effect, etc., so as to promote spheroidization transformation and shorten spheroidization. Annealing cycle, the effect of improving continuity
- Summary
- Abstract
- Description
- Claims
- Application Information
AI Technical Summary
Benefits of technology
Problems solved by technology
Method used
Image
Examples
Embodiment 1
[0026] Ф25mm high carbon chromium bearing steel round bar annealed production;
[0027] Invention composition: C: 0.97%, Mn: 0.34%, Si: 0.25%, Cr: 1.45%, P: 0.009%, S: 0.004%, Ni: 0.02%, Cu: 0.06%, Mo: 0.01%, Al : 0.010%, Ti: 0.0015%, [O]: 0.0006%, Ca: 0.0001%, As: 0.004%, Pb: 0.0002%, Sn: 0.003%; the balance is Fe and unavoidable impurities.
[0028] The steps of the present invention include furnace loading, heating and heating, primary isothermal, cooling, secondary isothermal, cooling out of the furnace, finishing and inspection.
[0029] (1) Through high-temperature diffusion and controlled rolling and controlled cooling, the 25mm round steel in the hot-rolled state is obtained, and the 25mm high-carbon chromium bearing steel round steel in the hot-rolled state is loaded into the roller hearth type continuous annealing furnace; wherein the roller hearth type continuous annealing furnace Stove, the heating source is natural gas, the upper and lower rows of radiant tubes are
Embodiment 2
[0038] Ф70mm high carbon chromium bearing steel round steel annealed production;
[0039] Invention composition: C: 0.98%, Mn: 0.33%, Si: 0.26%, Cr: 1.48%, P: 0.010%, S: 0.003%, Ni: 0.02%, Cu: 0.05%, Mo: 0.01%, Al : 0.013%, Ti: 0.0015%, [O]: 0.0005%, Ca: 0.0001%, As: 0.004%, Pb: 0.0002%, Sn: 0.003%; the balance is Fe and unavoidable impurities.
[0040] The steps of the present invention include furnace loading, heating and heating, primary isothermal, cooling, secondary isothermal, cooling out of the furnace, finishing and inspection.
[0041] (1) Through high-temperature diffusion and controlled rolling and controlled cooling, the hot-rolled 70mm round steel is obtained, and the hot-rolled 70mm high-carbon chromium bearing steel round steel is loaded into the roller hearth type continuous annealing furnace; wherein the roller hearth type continuous annealing furnace Stove, the heating source is natural gas, the upper and lower rows of radiant tubes are used for radiant heating
PUM
Property | Measurement | Unit |
---|---|---|
Depth | aaaaa | aaaaa |
Depth | aaaaa | aaaaa |
Abstract
Description
Claims
Application Information
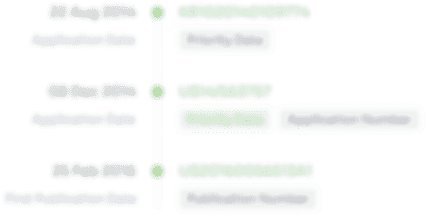
- R&D Engineer
- R&D Manager
- IP Professional
- Industry Leading Data Capabilities
- Powerful AI technology
- Patent DNA Extraction
Browse by: Latest US Patents, China's latest patents, Technical Efficacy Thesaurus, Application Domain, Technology Topic.
© 2024 PatSnap. All rights reserved.Legal|Privacy policy|Modern Slavery Act Transparency Statement|Sitemap