Process for manufacturing hydrophobized microporous film
a technology of hydrophobic microporous film and manufacturing process, which is applied in the direction of pretreatment surface, coating, and semiconductor/solid-state device details, etc., can solve the problems of increasing the time required for hydrophobic treatment, unable to provide sufficient hydrophobic effect of microporous film, and affecting etc. , to achieve the effect of reducing the elastic modulus of the microporous film, reducing the surface area
- Summary
- Abstract
- Description
- Claims
- Application Information
AI Technical Summary
Benefits of technology
Problems solved by technology
Method used
Image
Examples
first embodiment
[0025]A process for manufacturing a microporous film of the present embodiment will be described. FIG. 1 is a schematic diagram, illustrating a process for manufacturing a microporous film of the present embodiment. As shown in FIG. 1, a substrate 1 having an organic silica insulating film 2 formed thereon is disposed in an apparatus (not shown). The substrate 1 is heated by an irradiation of an infrared lamp 4 from the downward. A gaseous mixture 3 is supplied over the upside of the organic silica insulating film 2 formed on the substrate 1. Since the temperatures of the substrate 1 and the organic silica insulating film 2 are equal to or higher than the dew point and equal to or lower than the vaporizing temperature of a silylation gas contained in the gaseous mixture 3, the gaseous mixture 3 diffuses over the surface of the organic silica insulating film 2 and to the inside of the organic silica insulating film 2 to cause the adsorption of the silylation gas contained in the gaseous
example 1
[0061]A silicon substrate was coated with an aqueous mixture of siloxane, an acid, and an organic monomer, and the temperature of the silicon substrate was stepwise performed elevated from 100 degrees C. to 400 degrees C. within a nitrogen atmosphere. Such temperature-elevation caused formation of aggregated material of the organic monomer, and siloxane was polymerized so as to surround the aggregated material, and then the aggregated material of the organic monomer was thermally decomposed to form an organic silica insulating film having open type pores. The silicon substrate having the organic silica insulating film formed thereon was obtained in such way.
[0062]Next, the silicon substrate having the organic silica insulating film formed thereon was disposed in a vacuum chamber, and the chamber was evacuated to a vacuum of about 0.01 Pa by employing a dry pump.
[0063]The temperature of the silicon substrate was maintained at about 50 degrees C. with the infrared lamp, while the evacuat
example 2
[0078]The silicon substrate having the organic silica insulating film formed thereon was obtained similarly as in Example 1.
[0079]Next, the silicon substrate having the organic silica insulating film formed thereon was disposed in a vacuum chamber, and the chamber was evacuated to a vacuum of about 0.01 Pa by employing a dry pump.
[0080]The temperature of the silicon substrate was maintained at about 50 degrees C. with the infrared lamp, while the evacuation was continued.
[0081]In next, a gaseous mixture of tetramethyl cyclotetrasiloxane generated by vaporizing with a heating-type vaporizer and nitrogen carrier gas was supplied into the chamber at a rate of 2 liters per minute, the pressure in the chamber was maintained at 1 kPa to 30 kPa, and the silicon substrate was exposed to the gaseous mixture for 1 minute. Then, the supply of the gaseous mixture was stopped, and the temperature of the silicon substrate was elevated to a temperature of 400 degrees C. by increasing the output of th
PUM
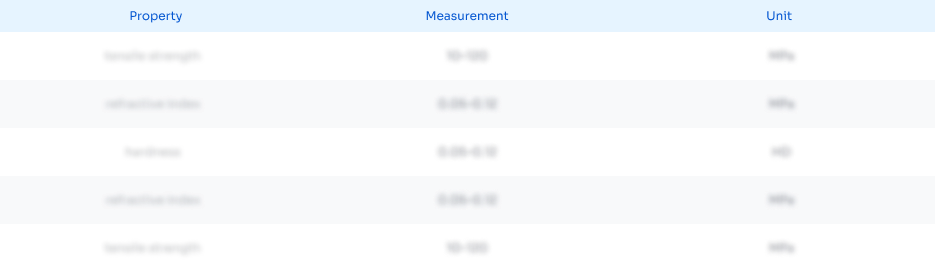
Abstract
Description
Claims
Application Information
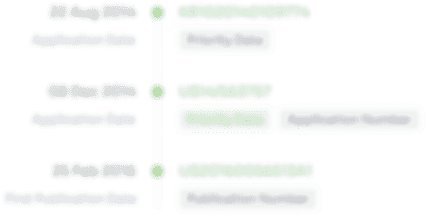
- R&D Engineer
- R&D Manager
- IP Professional
- Industry Leading Data Capabilities
- Powerful AI technology
- Patent DNA Extraction
Browse by: Latest US Patents, China's latest patents, Technical Efficacy Thesaurus, Application Domain, Technology Topic.
© 2024 PatSnap. All rights reserved.Legal|Privacy policy|Modern Slavery Act Transparency Statement|Sitemap