A kind of etching method of diffusion layer of crystalline silicon solar cell
A technology of solar cells and diffusion layers, applied in crystal growth, chemical instruments and methods, circuits, etc., to achieve the effect of reducing the number, easy etching process, and simple process
- Summary
- Abstract
- Description
- Claims
- Application Information
AI Technical Summary
Benefits of technology
Problems solved by technology
Method used
Examples
Embodiment 1
[0017] Step 1: Put the silicon wafer on which the diffusion layer has been formed into a thermal oxidation furnace, and deposit a silicon dioxide film with a thickness of 65 nm on the surface of the silicon wafer.
[0018] Step 2: Prepare a mixed solution of phosphoric acid and nitric acid with a molar ratio of 3:10, put the silicon chip into it for 55 seconds, so that the silicon chip and the solution fully react.
[0019] Step 3: Put the silicon chip into a 20% hydrofluoric acid solution, soak it for 60 seconds, then take it out and rinse it with deionized water for about 60 seconds.
[0020]
Embodiment 2
[0022] Step 1: Put the silicon wafer on which the diffusion layer has been formed into a thermal oxidation furnace, and deposit a silicon dioxide film with a thickness of 62nm on the surface of the silicon wafer.
[0023] Step 2: Prepare a mixed solution of phosphoric acid and nitric acid with a molar ratio of 2:10, put the silicon chip into it for 60 seconds, so that the silicon chip and the solution fully react.
[0024] Step 3: Put the silicon chip into a 20% hydrofluoric acid solution, soak it for 60 seconds, then take it out and rinse it with deionized water for about 60 seconds.
[0025]
Embodiment 3
[0027] Step 1: Put the silicon wafer on which the diffusion layer has been formed into a thermal oxidation furnace, and deposit a silicon dioxide film with a thickness of 63nm on the surface of the silicon wafer.
[0028] Step 2: Prepare a mixed solution with a molar ratio of phosphoric acid and nitric acid of 5:10, put the silicon chip into it for 62 seconds, so that the silicon chip can fully react with the solution.
[0029] Step 3: Put the silicon wafer into a 20% hydrofluoric acid solution, soak for 60 seconds, then take it out and rinse it with deionized water for about 60 seconds.
[0030]
PUM
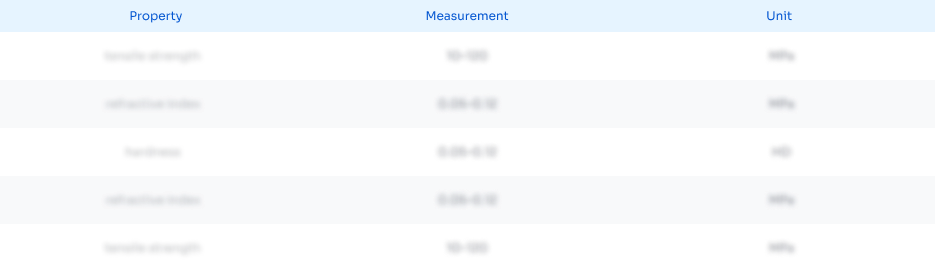
Abstract
Description
Claims
Application Information
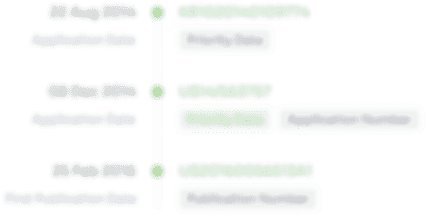
- R&D Engineer
- R&D Manager
- IP Professional
- Industry Leading Data Capabilities
- Powerful AI technology
- Patent DNA Extraction
Browse by: Latest US Patents, China's latest patents, Technical Efficacy Thesaurus, Application Domain, Technology Topic.
© 2024 PatSnap. All rights reserved.Legal|Privacy policy|Modern Slavery Act Transparency Statement|Sitemap