Catalytic oxidation pressure acid leaching decomposition method of nickel-molybdenum ore
A technology for catalytic oxidation and nickel-molybdenum ore, applied in the field of beneficiation and metallurgy, can solve the problems of toxic nitrogen oxides, large consumption of oxidants, high environmental protection pressure, etc., and achieve the effects of environmental protection, short process flow and low production cost
- Summary
- Abstract
- Description
- Claims
- Application Information
AI Technical Summary
Problems solved by technology
Method used
Examples
Example Embodiment
[0020] Example 1
[0021] Take 500g of -120 mesh nickel-molybdenum ore containing 2.1% molybdenum and 1.8% nickel, add 100g FeSO 4 As a catalyst, add H with a concentration of 1.5mol / L according to the solid-liquid ratio of 1:3g / ml 2 SO 4 The solution was mixed in a pressure reactor, oxygen was bubbled to 2.5Mpa, leached at 120°C for 2 hours, and liquid-solid separation was performed after cooling. In the leaching slag, elemental sulfur is recovered by evaporation; nickel and molybdenum are enriched in the incoming and outgoing liquids. In this example, the nickel leaching rate was 97.2%, and the molybdenum leaching rate was 98.7%.
Example Embodiment
[0022] Example 2
[0023] Take 1000g of -150 mesh nickel-molybdenum ore containing 1.6% molybdenum and 3.2% nickel, add 140g FeCl 2 As a catalyst, add HCl solution with a concentration of 4mol / L according to the solid-liquid ratio of 1:2g / ml, mix in the pressure reactor, blow air to 5.5Mpa, leaching at 180°C for 1.5h, and separate liquid-solid after cooling. Elemental sulfur exists in the leaching slag, and nickel and molybdenum are enriched in the incoming and outgoing liquids. In this example, the nickel leaching rate was 98.3%, and the molybdenum leaching rate was 98.9%. The leaching residue was vacuum evaporated at 210°C to obtain sulfur with a purity of 99.7%.
Example Embodiment
[0024] Example 3
[0025] Take 500g of -180 mesh nickel-molybdenum ore containing 3.5% molybdenum and 2.2% nickel, add 70g FeCl 3 As a catalyst, according to the solid-liquid ratio of 1:4g / ml, add HCl solution with a concentration of 3mol / L, mix in the pressure reactor, blow oxygen to 4.5Mpa, leaching at 160 ℃ for 3h, and separate the liquid and solid after cooling. In the leaching slag, the elemental sulfur is recovered by dissolving in the solvent; nickel and molybdenum are enriched in the incoming and outgoing liquid.
PUM
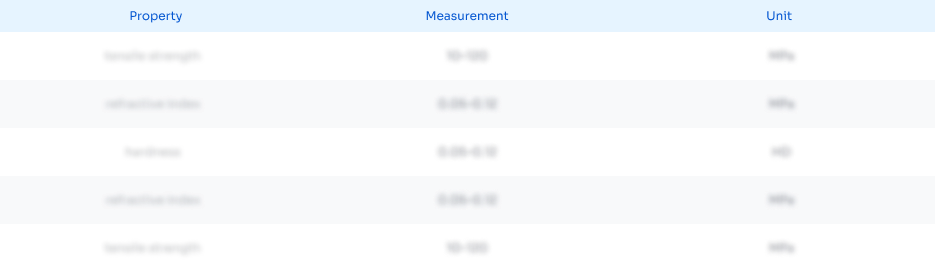
Abstract
Description
Claims
Application Information
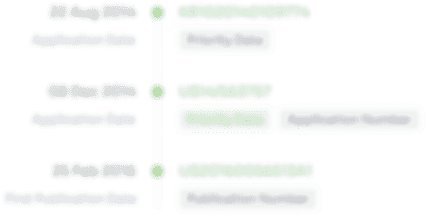
- R&D Engineer
- R&D Manager
- IP Professional
- Industry Leading Data Capabilities
- Powerful AI technology
- Patent DNA Extraction
Browse by: Latest US Patents, China's latest patents, Technical Efficacy Thesaurus, Application Domain, Technology Topic.
© 2024 PatSnap. All rights reserved.Legal|Privacy policy|Modern Slavery Act Transparency Statement|Sitemap