Novel thermoforming reinforcer and processing method thereof
A processing method and reinforcement technology, applied in the manufacture of tools, heat treatment equipment, quenching agents, etc., can solve the problems of poor corrosion resistance, reduced strength of reinforcements, heavy weight, etc., and achieve good corrosion resistance and fatigue resistance. Improvement of hardness and flexural strength, effect of reducing stress concentration problems
- Summary
- Abstract
- Description
- Claims
- Application Information
AI Technical Summary
Benefits of technology
Problems solved by technology
Method used
Image
Examples
Embodiment 1
[0019] The new thermoformed reinforcement in this embodiment is made of the following components by weight: 20 parts of iron, 3 parts of nano-silicon carbide particles, 3 parts of tungsten, 1 part of manganese, 2 parts of molybdenum, 3 parts of cobalt, 2 parts nickel, 1 part chromium, 3 parts vanadium, 2 parts titanium.
[0020] A processing method for a novel thermoformed reinforcement, comprising the following steps:
[0021] (1) Take 20 parts of powdered iron, 3 parts of nano-silicon carbide particles, 3 parts of tungsten, 1 part of manganese, 2 parts of molybdenum, 3 parts of cobalt, 2 parts of nickel, 1 part of chromium and 3 parts of vanadium in proportion by weight 1, 2 parts of titanium, pre-mix the powdery above-mentioned ingredients, mix and add to a high-speed mixer for stirring, the speed of the high-speed mixer is 300r / min, and the stirring time is 30-60min;
[0022] (2) Add the reinforcement raw materials mixed in step (1) into the heating furnace, fill the heati
Embodiment 2
[0030] The new thermoformed reinforcement in this embodiment is made of the following components by weight: 30 parts of iron, 5 parts of tungsten, 2 parts of manganese, 6 parts of molybdenum, 5 parts of cobalt, 3.5 parts of nickel, and 2 parts of chromium , 3 parts of cobalt, 5 parts of vanadium, and 4 parts of titanium.
[0031] A processing method for a novel thermoformed reinforcement, comprising the following steps:
[0032] (1) Take 30 parts of powdered iron, 5 parts of tungsten, 2 parts of manganese, 6 parts of molybdenum, 5 parts of cobalt, 3.5 parts of nickel, 2 parts of chromium, 3 parts of cobalt, 5 parts of vanadium, and 4 parts of titanium according to the weight ratio. Parts, the above-mentioned ingredients are pre-mixed, mixed and added to the high-speed mixer, the speed of the high-speed mixer is 300r / min, and the mixing time is 60min;
[0033] (2) Add the reinforcement raw materials mixed in step (1) into the heating furnace, fill the heating furnace with nitro
Embodiment 3
[0041] The new thermoformed reinforcement in this embodiment is made of the following components by weight: 25 parts of iron, 3.5 parts of tungsten, 1.5 parts of manganese, 3 parts of molybdenum, 3.5 parts of cobalt, 2.5 parts of nickel, and 1.5 parts of chromium , 4 parts of vanadium, 3 parts of titanium.
[0042] A processing method for a novel thermoformed reinforcement, comprising the following steps:
[0043] (1) Take 25 parts of powdered iron, 3.5 parts of tungsten, 1.5 parts of manganese, 3 parts of molybdenum, 3.5 parts of cobalt, 2.5 parts of nickel, 1.5 parts of chromium, 4 parts of vanadium and 3 parts of titanium according to the weight ratio. The ingredients are pre-mixed, and then added to the high-speed mixer after mixing. The speed of the high-speed mixer is 300r / min, and the mixing time is 30min;
[0044] (2) Add the reinforcement raw materials mixed in step (1) into the heating furnace, fill the heating furnace with nitrogen gas until all the impurity gases i
PUM
Property | Measurement | Unit |
---|---|---|
Yield strength | aaaaa | aaaaa |
Tensile strength | aaaaa | aaaaa |
Hardness | aaaaa | aaaaa |
Abstract
Description
Claims
Application Information
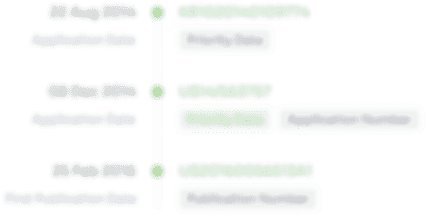
- R&D Engineer
- R&D Manager
- IP Professional
- Industry Leading Data Capabilities
- Powerful AI technology
- Patent DNA Extraction
Browse by: Latest US Patents, China's latest patents, Technical Efficacy Thesaurus, Application Domain, Technology Topic.
© 2024 PatSnap. All rights reserved.Legal|Privacy policy|Modern Slavery Act Transparency Statement|Sitemap