Preparation method of nitrogen doping pine nut shell based porous carbon material and application
A pine nut shell and nitrogen doping technology is applied in the field of porous materials, which can solve the problems of low specific surface area and low specific capacity of porous carbon materials, and achieve the effects of reducing production cost, increasing specific surface area and improving performance.
- Summary
- Abstract
- Description
- Claims
- Application Information
AI Technical Summary
Problems solved by technology
Method used
Image
Examples
Example Embodiment
[0031] Example 1
[0032] A method for preparing a nitrogen-doped pine nut shell-based porous carbon material, the method steps are as follows:
[0033] Step 1: Low-temperature carbonization of pine nut shells: Wash the pine nut shells, grind the pine nut shells into powder with a crusher after drying, and dry, then place them in a tube furnace for carbonization at 500°C for 2 hours, and then the product Filter, wash, dry, and grind to obtain the pine nut shell-based carbon material precursor;
[0034] Step 2: Material precursor activation: The pine nut shell-based carbon material precursor is mixed with urea and potassium hydroxide in a mass ratio of 1.0:3.0:3.0, put in 30ml of deionized water, fully stirred, and dried, protected by nitrogen Calcined at 700 ℃ for 2h to obtain the crude product of nitrogen-doped modified pine nut shell-based carbon material;
[0035] Step 3: Post-processing: soak the above crude product with 0.1M HCl solution, wash with deionized water, suction filter t
Example Embodiment
[0041] Example 2
[0042] A method for preparing a nitrogen-doped pine nut shell-based porous carbon material is as follows:
[0043] Step 1: Low-temperature carbonization of pine nut shells: Wash the pine nut shells, grind the pine nut shells into powder with a breaker after drying, and dry them, then place them in a tube furnace for carbonization at 450°C for 3 hours, and then the product Filter, wash, dry, and grind to obtain the pine nut shell-based carbon material precursor;
[0044] Step 2: Material precursor activation: The obtained material precursor is mixed with semicarbazide and sodium hydroxide in a mass ratio of 1.0:3.0:6.0, put in 30ml of deionized water and fully stirred, after drying, put it under nitrogen protection for 800 Calcined at ℃ for 6h to obtain the crude product of nitrogen-doped modified pine nut shell-based carbon material;
[0045] Step 3: Post-processing: soak the above crude product with 0.1M HCl solution, wash with deionized water, suction filter to neut
Example Embodiment
[0047] Example 3
[0048] A method for preparing a nitrogen-doped pine nut shell-based porous carbon material is as follows:
[0049] Step 1: Low-temperature carbonization of pine nut shells: Wash the pine nut shells, grind the pine nut shells into powder with a crusher after drying, and dry them, then place them in a tube furnace and carbonize them at a low temperature of 500°C for 1 hour, then the product Filter, wash, dry, and grind to obtain the precursor of nitrogen-doped pine nut shell-based carbon material;
[0050] Step 2: Material precursor activation: The obtained nitrogen-doped pine nut shell-based carbon material precursor is mixed with guanidine carbonate and potassium carbonate in a mass ratio of 1.0:3.0:1.5, put into 30ml of deionized water and fully stirred, after drying It is calcined at 700°C for 4 hours under the protection of nitrogen to obtain the crude product of nitrogen-doped modified pine nut shell-based carbon material;
[0051] Step 3: Post-processing: soak th
PUM
Property | Measurement | Unit |
---|---|---|
Specific surface area | aaaaa | aaaaa |
Average pore size | aaaaa | aaaaa |
Pore volume | aaaaa | aaaaa |
Abstract
Description
Claims
Application Information
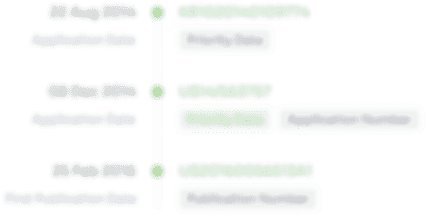
- R&D Engineer
- R&D Manager
- IP Professional
- Industry Leading Data Capabilities
- Powerful AI technology
- Patent DNA Extraction
Browse by: Latest US Patents, China's latest patents, Technical Efficacy Thesaurus, Application Domain, Technology Topic.
© 2024 PatSnap. All rights reserved.Legal|Privacy policy|Modern Slavery Act Transparency Statement|Sitemap