Preparation method of polyacrylonitrile-based hollow carbon fibers
A polyacrylonitrile-based and polyacrylonitrile technology is applied in the field of preparation of polyacrylonitrile-based hollow carbon fibers, which can solve the problems of high energy consumption, cumbersome process and high activation temperature, and achieves simplified process flow, shortened process flow, The effect of good application prospects
- Summary
- Abstract
- Description
- Claims
- Application Information
AI Technical Summary
Benefits of technology
Problems solved by technology
Method used
Image
Examples
Embodiment 1
[0051] At 30°C, dissolve alkali lignin and polyacrylonitrile in a mass ratio of 30:70 and a mass fraction of 20 wt% in dimethyl sulfoxide, mechanically stir until uniformly mixed, and then vacuum (vacuum degree is 0.08 MPa) at 60°C for 12 hours after defoaming treatment, then set aside for later use. Then, coagulate the spinning solution at 60°C through a 0.51mm spinneret in a coagulation bath at 50°C (the volume ratio of DMSO / water in the coagulation bath=20 / 80), and then at 80°C in pure After being drawn twice in water, the hollow hollow primary fiber was obtained. Wash the as-spun fibers in multi-stage water baths at 40, 50, and 60°C, and wash each stage for 12 hours, and then dry them in an oven at normal pressure to obtain hollow porous precursors. Next, the above precursor filaments were heated to 250° C. in air at a heating rate of 5° C. / min, and kept at 250° C. for 5 hours to obtain hollow hollow pre-oxidized fibers. Finally, the above-mentioned pre-oxidized fiber
Embodiment 2-8
[0053] The processing conditions in the embodiment are shown in Table 1, and all the other operating steps are the same as in Example 1. The results in the examples are shown in Table 2.
[0054] Process condition in table 1 embodiment 2-8
[0055]
[0056] Table 1 continues the processing conditions in the embodiment 2-8
[0057]
[0058] The result in the embodiment of table 2
[0059]
PUM
Property | Measurement | Unit |
---|---|---|
Average pore size | aaaaa | aaaaa |
Outer diameter | aaaaa | aaaaa |
Wall thickness | aaaaa | aaaaa |
Abstract
Description
Claims
Application Information
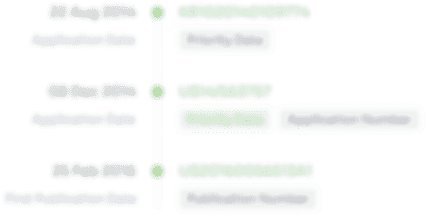
- R&D Engineer
- R&D Manager
- IP Professional
- Industry Leading Data Capabilities
- Powerful AI technology
- Patent DNA Extraction
Browse by: Latest US Patents, China's latest patents, Technical Efficacy Thesaurus, Application Domain, Technology Topic.
© 2024 PatSnap. All rights reserved.Legal|Privacy policy|Modern Slavery Act Transparency Statement|Sitemap