Preparation method of high strength, high modulus and high plasticity ceramic particle aluminum-based composite material
An aluminum-based composite material and ceramic particle technology, which is applied in the field of metallurgical materials, can solve the problems of inability to meet aerospace requirements and difficult processing of materials, and achieve the effects of high plasticity, simple process, high strength and elastic modulus
- Summary
- Abstract
- Description
- Claims
- Application Information
AI Technical Summary
Benefits of technology
Problems solved by technology
Method used
Image
Examples
Embodiment 1
[0026] Preparation:
[0027] The ceramic volume fraction of the composite material prepared by the method is controlled at 10-50% vol, and the preparation method is as follows:
[0028] S1 ingredients: According to the volume fraction and gradation theory, mix silicon carbide particles with different particle sizes evenly, and then fill them into the mold. The ratio of silicon carbide particles with a particle size of 200 mesh and a particle size of 800 mesh is 3:1;
[0029] S2 Heating the mold: put the mold into the heating furnace, heat the mold evenly at a rate of 15°C / min, and raise the temperature to 620°C;
[0030] S3 aluminum melting: put the aluminum alloy into the aluminum melting furnace for melting and casting, and vacuumize and stir.
[0031] S4 aluminum injection: move the heated mold to the hot press platform, and inject the aluminum solution in the aluminum melting furnace into the mold.
[0032] S5 hot pressing: adjust the hot press to 1MPa and start pressing
Embodiment 2
[0035] Preparation:
[0036] The ceramic volume fraction of the composite material prepared by the method is controlled at 10-50% vol, and the preparation method is as follows:
[0037] S1 ingredients: According to the volume fraction and gradation theory, mix silicon carbide particles with different particle sizes evenly, and then fill them into the mold. The ratio of silicon carbide particles with a particle size of 200 mesh and a particle size of 800 mesh is 3:1;
[0038] S2 Heating the mold: put the mold into the heating furnace, heat the mold evenly at a rate of 20°C / min, and raise the temperature to 620°C;
[0039] S3 aluminum melting: put the aluminum alloy into the aluminum melting furnace for melting and casting, and vacuumize and stir.
[0040] S4 aluminum injection: move the heated mold to the hot press platform, and inject the aluminum solution in the aluminum melting furnace into the mold.
[0041] S5 hot pressing: adjust the hot press to 1MPa and start pressing
Embodiment 3
[0044] Preparation:
[0045] The ceramic volume fraction of the composite material prepared by the method is controlled at 10-50% vol, and the preparation method is as follows:
[0046] S1 ingredients: According to the volume fraction and gradation theory, mix silicon carbide particles with different particle sizes evenly, and then fill them into the mold. The ratio of silicon carbide particles with a particle size of 200 mesh and a particle size of 800 mesh is 3:1;
[0047] S2 Heating the mold: put the mold into the heating furnace, heat the mold evenly at a rate of 18°C / min, and raise the temperature to 620°C;
[0048] S3 aluminum melting: put the aluminum alloy into the aluminum melting furnace for melting and casting, and vacuumize and stir.
[0049] S4 aluminum injection: move the heated mold to the hot press platform, and inject the aluminum solution in the aluminum melting furnace into the mold.
[0050] S5 hot pressing: adjust the hot press to 1 MPa and start pressing
PUM
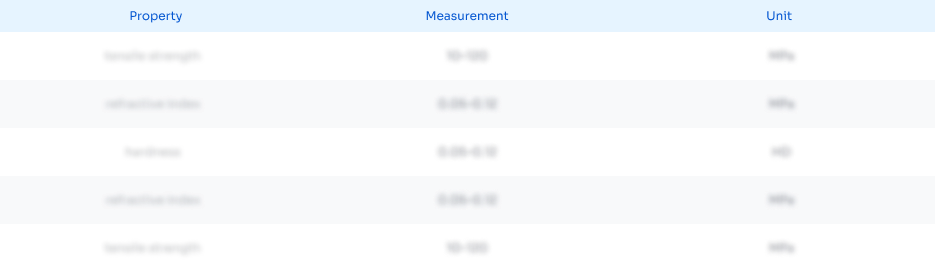
Abstract
Description
Claims
Application Information
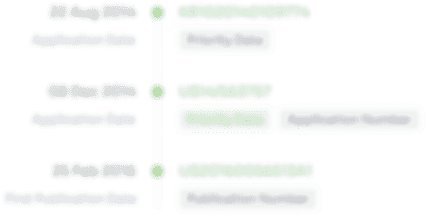
- R&D Engineer
- R&D Manager
- IP Professional
- Industry Leading Data Capabilities
- Powerful AI technology
- Patent DNA Extraction
Browse by: Latest US Patents, China's latest patents, Technical Efficacy Thesaurus, Application Domain, Technology Topic.
© 2024 PatSnap. All rights reserved.Legal|Privacy policy|Modern Slavery Act Transparency Statement|Sitemap