Acidic lithium slag-Portland cement-silica fume composite cementing material and preparation method thereof
A composite cementitious material and Portland cement technology, applied in the field of cementitious materials, can solve problems such as the inability to guarantee cement density and collapse, and achieve the effects of improving the flexural resistance, improving the quality of finished products, and accurately controlling the density
- Summary
- Abstract
- Description
- Claims
- Application Information
AI Technical Summary
Problems solved by technology
Method used
Examples
Embodiment 1
[0045] Including the following steps:
[0046] Step 1: Take 12 parts by weight of fly ash, 15 parts by weight of sludge, 2 parts by weight of oyster shell powder, 5 parts by weight of clay, 30 parts by weight of water and 10 parts by weight of easy-to-melt foaming particles, and mix them evenly. Parts by weight only represent the weight ratio of each component inside the lightweight filler, which is fired after granulation to obtain the lightweight filler;
[0047] Step one specifically includes:
[0048] (1) Take 12 parts by weight of fly ash, 15 parts by weight of sludge, 2 parts by weight of oyster shell powder, 5 parts by weight of clay and 30 parts by weight of water, and mix them uniformly to obtain a slurry;
[0049] (2) Uniformly mixing the slurry and the easily meltable foamed particles to obtain a mixed product;
[0050] (3) Preheating the mixed product once to make it initial set to obtain the initial set product;
[0051] (4) Crushing the initial setting product i...
Embodiment 2
[0059] Including the following steps:
[0060] Step 1: Take 35 parts by weight of fly ash, 25 parts by weight of sludge, 10 parts by weight of oyster shell powder, 20 parts by weight of clay, 50 parts by weight of water and 20 parts by weight of easy-to-melt foaming particles, and mix them evenly. Parts by weight only represent the weight ratio of each component inside the lightweight filler, which is fired after granulation to obtain the lightweight filler;
[0061] Step one specifically includes:
[0062] (1) Take 35 parts by weight of fly ash, 25 parts by weight of sludge, 10 parts by weight of oyster shell powder, 20 parts by weight of clay and 50 parts by weight of water, and mix them uniformly to obtain a slurry;
[0063] (2) Uniformly mixing the slurry and the easily meltable foamed particles to obtain a mixed product;
[0064] (3) Preheating the mixed product once to make it initial set to obtain the initial set product;
[0065] (4) Crushing the initial setting pro...
Embodiment 3
[0073] Including the following steps:
[0074] Step 1: Take 20 parts by weight of fly ash, 20 parts by weight of sludge, 8 parts by weight of oyster shell powder, 10 parts by weight of clay, 40 parts by weight of water and 15 parts by weight of easy-to-melt foaming particles, and mix them evenly. Parts by weight only represent the weight ratio of each component inside the lightweight filler, which is fired after granulation to obtain the lightweight filler;
[0075] Step one specifically includes:
[0076] (1) Take 20 parts by weight of fly ash, 20 parts by weight of sludge, 8 parts by weight of oyster shell powder, 10 parts by weight of clay and 40 parts by weight of water, and mix them uniformly to obtain a slurry;
[0077] (2) Uniformly mixing the slurry and the easily meltable foamed particles to obtain a mixed product;
[0078] (3) Preheating the mixed product once to make it initial set to obtain the initial set product;
[0079] (4) Crushing the initial setting produ...
PUM
Property | Measurement | Unit |
---|---|---|
volume | aaaaa | aaaaa |
particle diameter | aaaaa | aaaaa |
Abstract
Description
Claims
Application Information
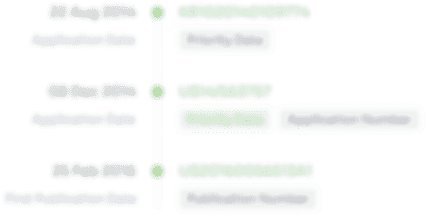
- R&D Engineer
- R&D Manager
- IP Professional
- Industry Leading Data Capabilities
- Powerful AI technology
- Patent DNA Extraction
Browse by: Latest US Patents, China's latest patents, Technical Efficacy Thesaurus, Application Domain, Technology Topic.
© 2024 PatSnap. All rights reserved.Legal|Privacy policy|Modern Slavery Act Transparency Statement|Sitemap