Transmission and clamping structure capable of realizing self-rotation of workpiece in vacuum furnace
A workpiece clamping and vacuum furnace technology, applied in furnaces, quenching devices, heat treatment furnaces, etc., can solve problems such as thermal stress, inconsistent workpiece temperature, and inconsistent temperature, and achieve the effect of improving consistency and reducing heat treatment distortion.
- Summary
- Abstract
- Description
- Claims
- Application Information
AI Technical Summary
Benefits of technology
Problems solved by technology
Method used
Image
Examples
specific Embodiment approach
[0018] The transmission and clamping structure of workpiece spin can be realized in the vacuum furnace of the present invention, and its preferred specific implementation mode is:
[0019] The structure is located in the cold zone of the vacuum furnace, including a driving gear II and a plurality of driven gears II meshing with each other. The driving gear II is fixedly connected to the driven gear I, and the driven gear I meshes with the driving gear I. The driving gear I is installed on the transmission shaft, the transmission shaft is connected to the output shaft of the drive reduction motor through a coupling, and the driven gear II is connected to the fixture clamping device;
[0020] The transmission shaft is fixed on the upper cover of the furnace through the support structure of the transmission shaft;
[0021] The driving gear II and the driven gear I are an integrated structure, and are installed on the upper cover of the furnace through the supporting structure of the
specific Embodiment
[0034] Such as figure 1 , figure 2 As shown, it includes driving gear motor 1, shaft sealing device 2, driving gear Ⅰ 3, driven gear Ⅰ 4, driving gear Ⅱ 5, driven gear Ⅱ 6, tooling and clamping device 7, coupling 8, transmission shaft 9, transmission shaft support Structure 10, driving gear II supporting structure 11, driven gear II supporting structure 12, wherein:
[0035] The drive deceleration motor is installed on the furnace shell, and the motor speed is adjustable.
[0036] The shaft sealing device is used to seal the output shaft of the driving geared motor to ensure reliable sealing of the driving system during vacuum heating and high-pressure gas quenching stages.
[0037] The driving gear I is a bevel gear, installed on the transmission shaft, and connected with the output shaft of the drive reduction motor through a coupling. The coupling can be quickly disassembled to meet the needs of loading, unloading and maintenance.
[0038] The driven gear I is a bevel gea
PUM
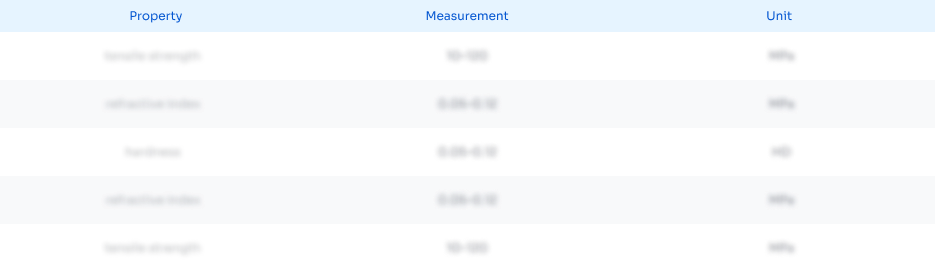
Abstract
Description
Claims
Application Information
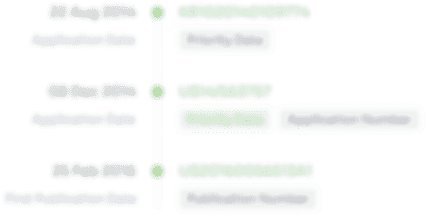
- R&D Engineer
- R&D Manager
- IP Professional
- Industry Leading Data Capabilities
- Powerful AI technology
- Patent DNA Extraction
Browse by: Latest US Patents, China's latest patents, Technical Efficacy Thesaurus, Application Domain, Technology Topic.
© 2024 PatSnap. All rights reserved.Legal|Privacy policy|Modern Slavery Act Transparency Statement|Sitemap