Avoiding hot cracks during laser welding of a workpiece stack-up assembly of aluminum alloy workpieces
a technology of aluminum alloy workpieces and stacking assemblies, which is applied in the field of laser welding, can solve the problems of hot cracks in laser weld joints, preventing the joint from reaching its maximum strength and other mechanical properties, and hot cracks
- Summary
- Abstract
- Description
- Claims
- Application Information
AI Technical Summary
Benefits of technology
Problems solved by technology
Method used
Examples
Embodiment Construction
[0034]The disclosed method of laser welding a workpiece stack-up assembly that includes two or more overlapping aluminum alloy workpieces can successfully fusion weld the workpieces together while counteracting the susceptibility of the resultant laser weld joint to hot-cracking. The disclosed method, more specifically, seeks to mitigate hot-cracking during the initial and / or final stages of laser beam advancement along a predefined weld path by controlling the power level of the laser beam so as to limit a line energy of the laser beam. By limiting the line energy in this way, excessive fusion of the aluminum alloy workpieces is prevented at the beginning and / or ending portions of the weld path. The line energy of the laser beam can be limited as needed by increasing the power level of the laser beam at a controlled rate during the initial stage of laser beam advancement along the weld path and / or decreasing the power level of the laser beam at a controlled rate during the final st...
PUM
Property | Measurement | Unit |
---|---|---|
wavelength | aaaaa | aaaaa |
focal length | aaaaa | aaaaa |
focal length | aaaaa | aaaaa |
Abstract
Description
Claims
Application Information
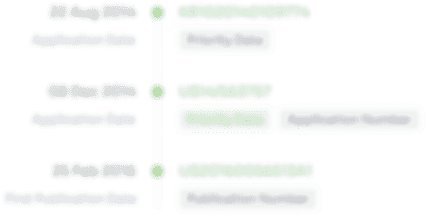
- R&D Engineer
- R&D Manager
- IP Professional
- Industry Leading Data Capabilities
- Powerful AI technology
- Patent DNA Extraction
Browse by: Latest US Patents, China's latest patents, Technical Efficacy Thesaurus, Application Domain, Technology Topic.
© 2024 PatSnap. All rights reserved.Legal|Privacy policy|Modern Slavery Act Transparency Statement|Sitemap