Preprocessing technical method of cotton linen and linen rayon gray fabrics
A technology for viscose and flax blanks and processing technology, which is used in textiles and papermaking, dry cleaning fiber products, bleaching products, etc. The effect of less consumption and shorter process time
- Summary
- Abstract
- Description
- Claims
- Application Information
AI Technical Summary
Problems solved by technology
Method used
Examples
Embodiment 1
[0022] A pretreatment process of cotton flax and sticky flax gray cloth in this embodiment includes the following process steps: gray cloth singeing→water washing→cold stacking, wherein the cold stacking process refers to rolling descouring enzyme additives at a controlled water temperature of 50°C , The liquid rolling rate is 90%, two rolling and two dipping, and the fabric is coiled and rotated on the A-frame at 8 rpm, and stacked at room temperature for 20 hours. Descaling enzyme auxiliary agent is prepared from the following raw materials in weight percentage: desizing enzyme 3%, purchased from Suzhou Baisheng Chemical Co., Ltd., the desizing enzyme model is TC-2000; flax degumming enzyme 10%, purchased from Kangdi En Biological Group, the model is the flax degumming enzyme of YL-01; Neutral cellulase 0.5%, purchased from Kang Dien Biological Group, the model is the neutral cellulase of KDN-F2; High-efficiency penetrant 3%, purchased from Hangzhou Electrochemical Group, hi...
Embodiment 2
[0024] A pretreatment process of cotton flax and sticky flax gray cloth in this embodiment includes the following process steps: gray cloth singeing→water washing→cold stacking, wherein the cold stacking process refers to rolling descouring enzyme additives at a controlled water temperature of 60°C , The liquid rolling rate is 100%, two rolling and two dipping, and the fabric is coiled and rotated on the A-frame at 8 rpm, and stacked at room temperature for 24 hours. Descaling enzyme auxiliary agent is prepared from the following raw materials in weight percentage: desizing enzyme 5%, purchased from Suzhou Baisheng Chemical Co., Ltd., the desizing enzyme model is TC-2000; flax degumming enzyme 15%, purchased at Kangdi En Biological Group, the model is the flax degumming enzyme of YL-01; Neutral cellulase 2%, purchased from Kang Dien Biological Group, the model is the neutral cellulase of KDN-F2; High-efficiency penetrant 5%, purchased from Hangzhou Electrochemical Group, high-...
Embodiment 3
[0026] A pretreatment process of cotton flax and sticky flax gray cloth in this embodiment includes the following process steps: gray cloth singeing→water washing→cold stacking, wherein the cold stacking process refers to rolling descouring enzyme additives at a controlled water temperature of 55°C , liquid rolling rate of 95%, two rolling and two dipping, while the fabric is coiled and rotated on the A-frame, 8 revolutions per minute, and stacked at room temperature for 22 hours. Descaling enzyme auxiliary agent is prepared from the following raw materials in weight percentage: desizing enzyme 4%, purchased from Suzhou Baisheng Chemical Co., Ltd., the desizing enzyme model is TC-2000; flax degumming enzyme 12%, purchased from Kangdi En biological group, the model is the flax degumming enzyme of YL-01; Neutral cellulase 1%, purchased from Kang Dien biological group, the model is the neutral cellulase of KDN-F2; High-efficiency penetrant 4%, purchased at Hangzhou Electrochemica...
PUM
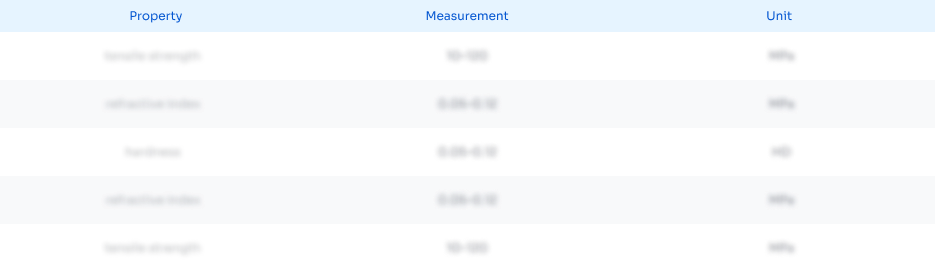
Abstract
Description
Claims
Application Information
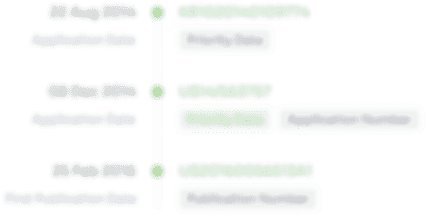
- R&D Engineer
- R&D Manager
- IP Professional
- Industry Leading Data Capabilities
- Powerful AI technology
- Patent DNA Extraction
Browse by: Latest US Patents, China's latest patents, Technical Efficacy Thesaurus, Application Domain, Technology Topic.
© 2024 PatSnap. All rights reserved.Legal|Privacy policy|Modern Slavery Act Transparency Statement|Sitemap