Production method of ceramic ferrule
A technology of ceramic ferrule and stabilized zirconia, which is applied in the direction of coupling of optical waveguides, can solve the problems of easy deformation of zirconia ceramics, complicated process, difficulty in ensuring accuracy, etc., to ensure the strength of green body and the uniformity of sintered body. And the effect of high strength, short degreasing cycle and improved precision
- Summary
- Abstract
- Description
- Claims
- Application Information
AI Technical Summary
Problems solved by technology
Method used
Examples
Example Embodiment
[0038] The embodiment of the present invention discloses a preparation method of a ceramic ferrule, comprising the following steps:
[0039] Step a) mixing strontium oxide, molybdenum oxide, cerium oxide and zirconia, pre-calcining, then adding oleic acid, magnesia and nano-silicon oxide, mixing by ball milling, and obtaining partially stabilized zirconia powder after sieving;
[0040] Step b) The partly stabilized zirconia powder, dibutyl phthalate, ethylene-vinyl acetate copolymer, zinc stearate, 3-methacryloxypropylmethyldimethoxysilane, poly Olefin elastomer, polypropylene, microcrystalline wax, polyethylene wax and oleic acid are mixed, added to a mixer for mixing, and a gelatinous substance is obtained;
[0041] Step c) compressing the gelatinous substance into tablets, pulverizing it, and obtaining a blank after injection molding;
[0042] Step d) immersing the blank in gasoline, and then performing degreasing treatment and sintering treatment in sequence to obtain a cera
Example Embodiment
[0087] Example 1
[0088] Step 1. Mix 1 part by weight of strontium oxide, 1 part by weight of molybdenum oxide, 3 parts by weight of cerium oxide and 93 parts by weight of zirconium oxide, pre-calcine at 1000 ° C, add 10 parts by weight of oleic acid , and then add 1 weight part of magnesia and 1 weight part of nano-silicon oxide, carry out ball milling and mixing, and sieve to obtain partially stabilized zirconia powder.
[0089] Step 2. Mix the partially stabilized zirconia powder prepared above with an organic carrier in a certain proportion. The raw materials used in this step include in parts by weight:
[0090]
[0091] Partially stabilized zirconia powder, dibutyl phthalate, ethylene-vinyl acetate copolymer, zinc stearate, 3-methacryloxypropylmethyldimethoxysilane, polyolefin Elastomer, polypropylene, microcrystalline wax, polyethylene wax, and oleic acid were added into a mixer according to the ratio for mixing. The mixing temperature was 180° C., and the mixing time
Example Embodiment
[0113] Example 2
[0114] Step 1. Mix 1 part by weight of strontium oxide, 1 part by weight of molybdenum oxide, 3 parts by weight of cerium oxide and 93 parts by weight of zirconium oxide, pre-calcine at 900 ° C, add 10 parts by weight of oleic acid , and then add 1 weight part of magnesia and 1 weight part of nano-silicon oxide, carry out ball milling and mixing, and sieve to obtain partially stabilized zirconia powder.
[0115] Step 2. Mix the partially stabilized zirconia powder prepared above with an organic carrier in a certain proportion. The raw materials used in this step include in parts by weight:
[0116]
[0117]
[0118] Partially stabilized zirconia powder, dibutyl phthalate, ethylene-vinyl acetate copolymer, zinc stearate, 3-methacryloxypropylmethyldimethoxysilane, polyolefin Elastomer, polypropylene, microcrystalline wax, polyethylene wax, and oleic acid were added into a mixer according to the ratio for mixing. The mixing temperature was 180° C., and the
PUM
Property | Measurement | Unit |
---|---|---|
Thickness | aaaaa | aaaaa |
Particle size | aaaaa | aaaaa |
Outer diameter | aaaaa | aaaaa |
Abstract
Description
Claims
Application Information
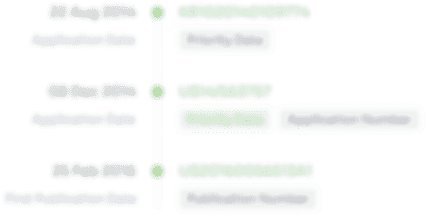
- R&D Engineer
- R&D Manager
- IP Professional
- Industry Leading Data Capabilities
- Powerful AI technology
- Patent DNA Extraction
Browse by: Latest US Patents, China's latest patents, Technical Efficacy Thesaurus, Application Domain, Technology Topic.
© 2024 PatSnap. All rights reserved.Legal|Privacy policy|Modern Slavery Act Transparency Statement|Sitemap