Multilayer natural fiber sheet and thermoplastic plastic composite material, and preparation method thereof
A thermoplastic and natural fiber technology, applied in the field of composite materials and their preparation, to achieve the effects of enhancing tensile and bending properties, reducing impact strength, and huge industrial application prospects
- Summary
- Abstract
- Description
- Claims
- Application Information
AI Technical Summary
Problems solved by technology
Method used
Examples
Embodiment 1
[0043] (1) Preparation of natural fiber sheet:
[0044] 1.1) take bamboo fiber as natural fiber, cut longer bamboo fiber to 10 mm with paper cutter to facilitate dispersion;
[0045] 1.2) with the hydroxyethyl cellulose solution as the dispersant solution, after the hydroxyethyl cellulose solution is blended with the bamboo fiber that the length is cut short, the volume ratio between the hydroxyethyl cellulose solution and the fiber is 1:50, The volume ratio of the dispersant contained in the solution to the bamboo fiber is 1:1, and the concentration of the dispersant in the solution is 2g / L and fully dried to remove moisture;
[0046] 1.3) Add the dried mixture into distilled pure water, and then disperse it with ultrasonic waves. The dispersion time is 5 minutes, and the treatment temperature is 30 degrees Celsius;
[0047] 1.4) Use a metal filter to filter out the moisture and most of the dispersant in the dispersed suspension, and wash with pure water to remove the remain...
Embodiment 2
[0057] (1) flax fiber sheet preparation:
[0058] 1.1) take flax fiber as natural fiber, cut longer bamboo fiber to 20 millimeters so that disperse processing with paper cutter;
[0059] 1.2) After the hydroxyethyl cellulose solution is blended with the flax fibers cut in length, the volume ratio between the dispersant solution and the fibers is 1:500, and the volume ratio of the dispersant contained in the solution to the flax fibers is 1: 1. The concentration of the dispersant in the solution is 200mg / L and fully dried to remove moisture;
[0060] 1.3) Add the dried mixture into distilled pure water, and then disperse it with ultrasonic waves;
[0061] 1.4) Use a metal filter to filter out the water and most of the dispersant in the dispersed suspension, and wash with pure water to remove the remaining 90% of the dispersant;
[0062] 1.5) Dry the filter screen and the bamboo fiber on it, and remove the dried flax fiber to obtain the flax fiber sheet.
[0063] (2) Composite ...
Embodiment 3
[0070] (1) Preparation of natural fiber sheet:
[0071] 1.1) take bamboo fiber as natural fiber, cut longer bamboo fiber to 10 mm with paper cutter to facilitate dispersion;
[0072] 1.2) after the hydroxyethyl cellulose solution is blended with the bamboo fiber that the length cuts short, the volume ratio between the dispersant solution and the fiber is 1:100, and the volume ratio of the dispersant contained in the solution and the bamboo fiber is 1: 1. The concentration of the dispersant in the solution is 1g / L and fully dried to remove moisture;
[0073] 1.3) Add the dried mixture into distilled pure water, and then disperse it with ultrasonic waves;
[0074] 1.4) Use a metal filter to filter out the moisture and most of the dispersant in the dispersed suspension, and wash with pure water to remove the remaining 95% of the dispersant;
[0075] 1.5) Dry the filter screen and the bamboo fiber on it, and remove the dried bamboo fiber to obtain a bamboo fiber sheet.
[0076]...
PUM
Property | Measurement | Unit |
---|---|---|
softening point | aaaaa | aaaaa |
diameter | aaaaa | aaaaa |
length | aaaaa | aaaaa |
Abstract
Description
Claims
Application Information
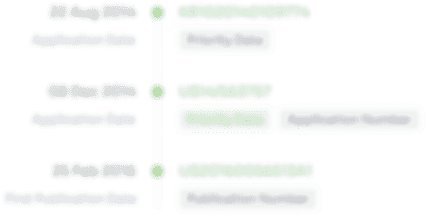
- R&D Engineer
- R&D Manager
- IP Professional
- Industry Leading Data Capabilities
- Powerful AI technology
- Patent DNA Extraction
Browse by: Latest US Patents, China's latest patents, Technical Efficacy Thesaurus, Application Domain, Technology Topic.
© 2024 PatSnap. All rights reserved.Legal|Privacy policy|Modern Slavery Act Transparency Statement|Sitemap