Anti-flaming viscose and method for preparing anti-flaming viscose by grafting melamine with oxidized viscose
A technology of flame retardant viscose fiber and viscose fiber, applied in fiber processing, plant fiber, flame retardant fiber and other directions, can solve problems such as mechanical properties decline, achieve good coloring ability, low flame retardant ratio, limit The effect of high oxygen index
- Summary
- Abstract
- Description
- Claims
- Application Information
AI Technical Summary
Benefits of technology
Problems solved by technology
Method used
Examples
Embodiment 1
[0050] 1. Preparation of pretreated viscose fiber
[0051] Prepare a sodium hydroxide solution with a mass concentration of 0.5%, add viscose fiber to the above sodium hydroxide solution, add 3g of viscose fiber per 100ml of sodium hydroxide solution, heat to boiling, keep boiling for 40min, take it out, wash with a large amount of water 6 times, dry and set aside.
[0052] 2. Preparation of oxidized viscose fiber
[0053] First prepare a dilute nitric acid solution with a concentration of 0.5% by volume, place it in a sandwich reactor with a ventilation coil at the bottom, and then disperse the pretreated fibers in the pretreated fiber mass / dilute nitric acid solution volume ratio of 1kg:50L. In the dilute nitric acid solution, ventilate and stir, the ventilating rate is 8-20 times / hour of the volume of the dilute nitric acid solution, heat up to 60°C, and react at constant temperature for 3 hours. The oxidation rate reaches 12%. After the reaction is over, take out the f
Embodiment 2
[0061] 1. Preparation of pretreated viscose fiber
[0062] Prepare a sodium hydroxide solution with a mass concentration of 0.4%, add viscose fiber to the above sodium hydroxide solution, add 8g of viscose fiber per 100ml of sodium hydroxide solution, heat to boiling, keep boiling for 120min, take it out, wash with a large amount of water Take it out to dry 8 times and set aside.
[0063] 2. Preparation of oxidized viscose fiber
[0064] First prepare a dilute nitric acid solution with a concentration of 3% by volume, place it in a sandwich reactor with a ventilation coil at the bottom, and then disperse the pretreated fibers in the pretreated fiber mass / dilute nitric acid solution volume ratio of 1kg:30L. In the dilute nitric acid solution, the volume of aeration and agitation is 8-20 times / hour of the volume of the dilute nitric acid, the temperature is raised to 70 degrees, and the reaction is carried out at constant temperature for 2 hours. The oxidation rate reaches 11
Embodiment 3
[0072] 1. Preparation of pretreated viscose fiber
[0073] Prepare a sodium hydroxide solution with a mass concentration of 0.6%, add viscose fiber to the above sodium hydroxide solution, add 5g of viscose fiber per 100ml of sodium hydroxide solution, heat to boiling, keep boiling for 80min, take it out, wash with a large amount of water 8 times, take out and dry, set aside.
[0074] 2. Preparation of oxidized viscose fiber
[0075] First prepare a dilute nitric acid solution with a concentration of 0.8% by volume, place it in a sandwich reactor with a ventilation coil at the bottom, and then disperse the pretreated fibers in the pretreated fiber mass / dilute nitric acid solution volume ratio of 1kg:40L. In the dilute nitric acid solution, the volume of aeration and agitation is 8-20 times / hour of the volume of the dilute nitric acid, the temperature is raised to 80°C, and the reaction is performed at a constant temperature for 1 hour. The oxidation rate reaches 9%. After t
PUM
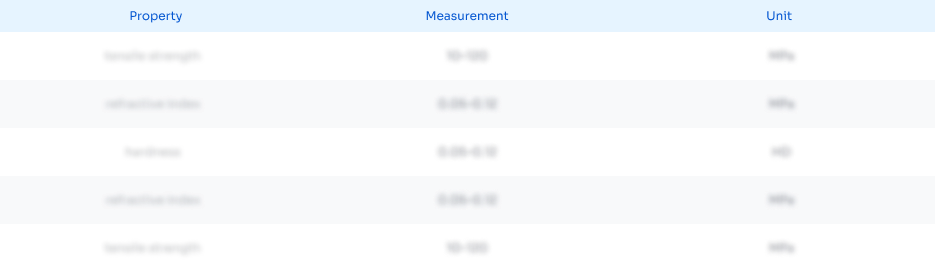
Abstract
Description
Claims
Application Information
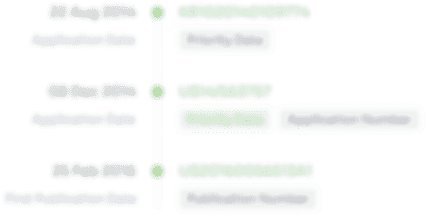
- R&D Engineer
- R&D Manager
- IP Professional
- Industry Leading Data Capabilities
- Powerful AI technology
- Patent DNA Extraction
Browse by: Latest US Patents, China's latest patents, Technical Efficacy Thesaurus, Application Domain, Technology Topic.
© 2024 PatSnap. All rights reserved.Legal|Privacy policy|Modern Slavery Act Transparency Statement|Sitemap