Warm and cold composite forging production process for hollow shaft sleeve of transmission shaft of SUV (sports utility vehicle)
A production process and transmission shaft technology, applied in the field of forging processing, can solve the problems of inability to adapt to the development trend, cracked hollow shaft sleeves, poor material compactness, etc., and achieve the effect of shortening the production cycle, good internal organization, and good mechanical properties of products.
- Summary
- Abstract
- Description
- Claims
- Application Information
AI Technical Summary
Benefits of technology
Problems solved by technology
Method used
Image
Examples
Embodiment Construction
[0016] The technical solutions of the present invention will be further described in detail below through embodiments and in conjunction with the accompanying drawings.
[0017] Example: see figure 1 and 2 As shown in the figure, a hollow shaft sleeve for a drive shaft of an SUV passenger car has a hollow cylindrical structure and is provided with an inner hole 1, an open end 4 and a closed end 3. The depth of the inner hole 1 reaches 180mm, and the inner cavity is a spline 2 structure. , the depth reaches 180mm, which is mainly used in passenger car steering system. see image 3 As shown in the figure, the production process includes the following steps: (1) cutting material: use a circular sawing machine to cut out the metal bar according to the drawing; (2) shot blasting: the prepared billet is shot blasted to remove the oxide scale on the surface; (3) graphite coating: the billet is Heating to 220°C±20°C, and then coating the surface with dilute graphite to prevent decarbu
PUM
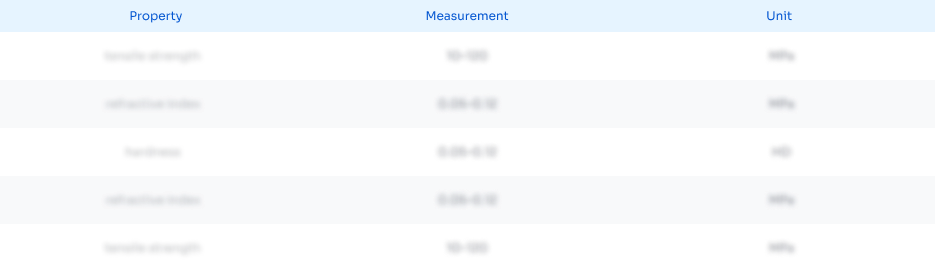
Abstract
Description
Claims
Application Information
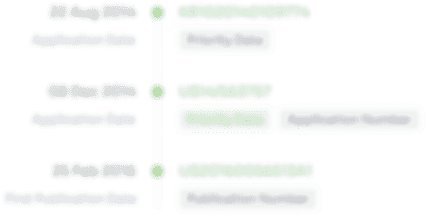
- R&D Engineer
- R&D Manager
- IP Professional
- Industry Leading Data Capabilities
- Powerful AI technology
- Patent DNA Extraction
Browse by: Latest US Patents, China's latest patents, Technical Efficacy Thesaurus, Application Domain, Technology Topic.
© 2024 PatSnap. All rights reserved.Legal|Privacy policy|Modern Slavery Act Transparency Statement|Sitemap