Fe3O4/CuO/pSiO2 catalyst and preparation method thereof
A catalyst, fe3o4 technology, applied in the direction of metal/metal oxide/metal hydroxide catalyst, physical/chemical process catalyst, chemical instrument and method, etc., can solve the problems of increased separation difficulty, catalyst loss, complex equipment, etc. Achieve the effects of improving recycling rate, prolonging service life, reducing production and maintenance costs
- Summary
- Abstract
- Description
- Claims
- Application Information
AI Technical Summary
Problems solved by technology
Method used
Image
Examples
Embodiment 1
[0026] (1) Fe 3 o 4 Preparation of magnetic microspheres: Weigh a certain amount of FeCl 3 ·6H 2 O was dissolved in deionized water with a concentration of 0.24mol / L, stirred at room temperature and continuously fed with high-purity nitrogen gas, the stirring rate was 280rpm, the stirring time was 40min, and an appropriate amount of FeCl was added 2 4H 2 O, and continue to react for 30min; raise the temperature to 80°C, and quickly add a certain amount of NH 3 ·H 2 O (containing ammonia 25~28%), in order to increase the hydrophilicity of its surface, inject 1.2mol / L citric acid solution drop by drop; 3 o 4 magnetic microspheres. Among them, FeCl 2 4H 2 O, FeCl 3 ·6H 2 O. The molar ratio of ammonia water to citric acid is about 1:2:200:2.
[0027] Weigh a certain amount of PVP (molecular weight 58,000) and dissolve it in deionized water to prepare a solution with a concentration of 3.6mol / L; secondly, add an appropriate amount of the above-prepared Fe 3 o 4 Magne...
Embodiment 2
[0033] (1) Fe 3 o 4 Preparation of magnetic microspheres: Weigh a certain amount of FeCl 3 ·6H 2 O was dissolved in deionized water with a concentration of 0.20mol / L, stirred at room temperature and continuously fed with high-purity nitrogen, the stirring rate was 300rpm, the stirring time was 30min, and an appropriate amount of FeCl was added 2 4H 2 O, and continue to react for 40min; heat up to 80°C, and quickly add a certain amount of NH 3 ·H 2 O (containing ammonia 25~28%), in order to increase its surface hydrophilicity, inject 1.1mol / L citric acid solution drop by drop; after the dropwise addition, react for 70min; vacuum dry to obtain Fe 3 o 4 magnetic microspheres. Among them, FeCl 2 4H 2 O, FeCl 3 ·6H 2 O. The molar ratio of ammonia water to citric acid is about 1:2:200:2.
[0034] Weigh a certain amount of PVP (molecular weight 58,000) and dissolve it in deionized water to prepare a solution with a concentration of 4.0mol / L; secondly, add an appropriate ...
Embodiment 3
[0040] (1) Fe 3 o 4 Preparation of magnetic microspheres: Weigh a certain amount of FeCl 3 ·6H 2 O was dissolved in deionized water with a concentration of 0.22mol / L, stirred at room temperature and continuously fed with high-purity nitrogen, the stirring rate was 310rpm, the stirring time was 25min, and an appropriate amount of FeCl was added 2 4H 2 O, and continue to react for 25min; heat up to 80°C, quickly add a certain amount of NH 3 ·H 2 O (containing ammonia 25~28%), in order to increase its surface hydrophilicity, inject 1.2mol / L citric acid solution drop by drop; 3 o 4 magnetic microspheres. Among them, FeCl 2 4H 2 O, FeCl 3 ·6H 2 O. The molar ratio of ammonia water to citric acid is about 1:2:200:2.
[0041] Weigh a certain amount of PVP (molecular weight 58000) and dissolve it in deionized water to prepare a solution with a concentration of 3.8mol / L; secondly, add an appropriate amount of the above-prepared Fe 3 o 4 Magnetic microspheres, ultrasonical...
PUM
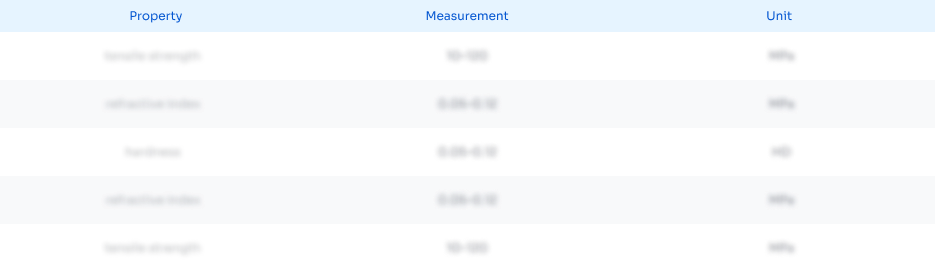
Abstract
Description
Claims
Application Information
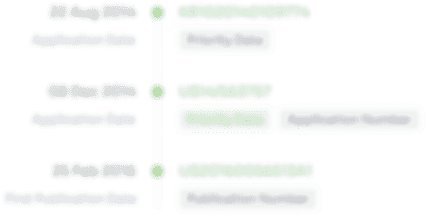
- R&D Engineer
- R&D Manager
- IP Professional
- Industry Leading Data Capabilities
- Powerful AI technology
- Patent DNA Extraction
Browse by: Latest US Patents, China's latest patents, Technical Efficacy Thesaurus, Application Domain, Technology Topic.
© 2024 PatSnap. All rights reserved.Legal|Privacy policy|Modern Slavery Act Transparency Statement|Sitemap