Bromine-carbon flame-retardant type acrylate ester waterproof coating and preparation method thereof
An acrylate and waterproof coating technology, applied in fire-resistant coatings, coatings, etc., can solve the problems of unsustainable flame retardant performance, unsatisfactory flame retardant effect, easy reduction of oxygen index, etc., and achieve large-scale production and broad market. Application prospect, good durability effect
- Summary
- Abstract
- Description
- Claims
- Application Information
AI Technical Summary
Problems solved by technology
Method used
Image
Examples
Embodiment 1
[0045] (1) Add 2kg of XL-70, 0.1kg of K12, 15kg of butyl acrylate, 5kg of isooctyl acrylate, 10kg of styrene, 7kg of pentabromobenzyl acrylate, 1kg of methyl methacrylate and 50kg of deionized water into the reaction vessel , and stir evenly to obtain a pre-emulsion.
[0046] (2) Take a pre-emulsion with 30% of the total mass of the pre-emulsion obtained in step (1), heat it up to 65° C., add 0.7 kg of ammonium persulfate quickly at one time, stir, and react at 80° C. for 5 minutes.
[0047] (3) Heat the mixed system of step (2) to 85°C, drop the remaining pre-emulsion therein, and then add dropwise the aqueous solution of ammonium persulfate (mixed 1.4kg ammonium persulfate and 10kg deionized water) ), the two-step dropwise addition takes a total of 1.5h, and after the dropwise addition, it is incubated at 85°C for 0.7h.
[0048] (4) Cool down the mixing system in step (3) to 40° C., add ammonia water with a mass concentration of 1% to adjust the pH of the system to 7.5-8.5,...
Embodiment 2
[0051] (1) Add 4kg of XL-70, 0.4kg of K12, 25kg of butyl acrylate, 10kg of isooctyl acrylate, 25kg of styrene, 15kg of pentabromobenzyl acrylate, 3kg of methyl methacrylate and 60kg of deionized water into the reaction vessel , and stir evenly to obtain a pre-emulsion.
[0052] (2) Take a pre-emulsion with 50% of the total mass of the pre-emulsion obtained in step (1), heat it up to 65° C., add 1.3 kg of ammonium persulfate quickly at one time, stir, and react at 85° C. for 15 minutes.
[0053] (3) Heat the mixed system of step (2) to 90°C, drop the remaining pre-emulsion therein, and then add dropwise the aqueous solution of ammonium persulfate (mixed 2.6kg ammonium persulfate and 20kg deionized water) ), the two-step dropwise addition takes a total of 2.5h, and after the dropwise addition, it is incubated at 90°C for 1.3h.
[0054] (4) Cool down the mixing system in step (3) to 50°C, add ammonia water with a mass concentration of 1% to adjust the pH of the system to 7.5-8.5...
Embodiment 3
[0057] (1) Add 3kg of XL-70, 0.2kg of K12, 20kg of butyl acrylate, 7kg of isooctyl acrylate, 15kg of styrene, 10kg of pentabromobenzyl acrylate, 2kg of methyl methacrylate and 55kg of deionized water into the reaction vessel , and stir evenly to obtain a pre-emulsion.
[0058] (2) Take a pre-emulsion with 40% of the total mass of the pre-emulsion obtained in step (1), heat it up to 65° C., add 1 kg of ammonium persulfate quickly at one time, stir, and react at 82° C. for 10 minutes.
[0059] (3) Heat the mixed system of step (2) to 86°C, drop the remaining pre-emulsion therein, and then add the aqueous solution of ammonium persulfate (by mixing 2kg of ammonium persulfate with 15kg of deionized water) , the two-step dropwise addition takes a total of 2h, and after the dropwise addition is completed, it is incubated at 86°C for 1h.
[0060] (4) Cool down the mixing system in step (3) to 45°C, add ammonia water with a mass concentration of 1% to adjust the pH of the system to 7....
PUM
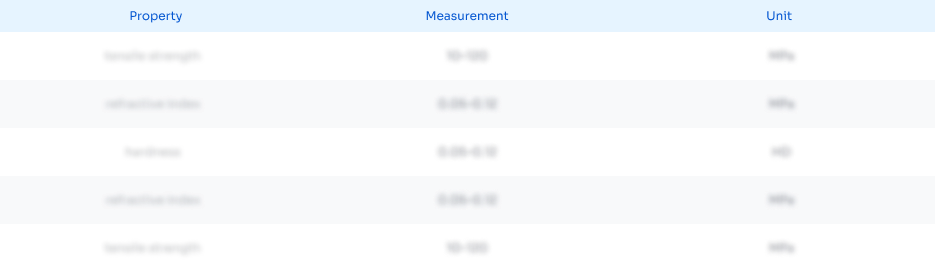
Abstract
Description
Claims
Application Information
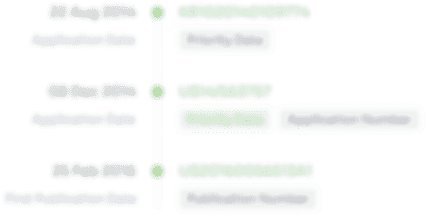
- R&D Engineer
- R&D Manager
- IP Professional
- Industry Leading Data Capabilities
- Powerful AI technology
- Patent DNA Extraction
Browse by: Latest US Patents, China's latest patents, Technical Efficacy Thesaurus, Application Domain, Technology Topic.
© 2024 PatSnap. All rights reserved.Legal|Privacy policy|Modern Slavery Act Transparency Statement|Sitemap