Coating roller, and application and preparation method thereof
A technology of coating rollers and coatings, which is applied to the device for coating liquid on the surface, coatings, special surfaces, etc. It can solve the problem that the working life is only 1-3 months, the pattern retention time is not long, and the coating pattern is not good. Clear and other problems, to achieve the effect of reducing the number of times of equipment shutdown and changing rolls, clear patterns, and long retention time
- Summary
- Abstract
- Description
- Claims
- Application Information
AI Technical Summary
Benefits of technology
Problems solved by technology
Method used
Image
Examples
preparation example Construction
[0028] The present invention also provides a method for preparing the above-mentioned coating roller, which includes the following steps:
[0029] Before forming the wear-resistant coating, roughen the coating roll substrate;
[0030] Preferably, the roughening treatment is performed by sandblasting to make the surface roughness of the coating roller substrate Ra4μm-Ra6μm;
[0031] More preferably, the sand material used for sandblasting is 150#-240# alumina or silicon carbide particles;
[0032] More preferably, sandblasting is processed by a supersonic flame spray system.
[0033] The roughening treatment can remove the residual oxides on the surface of the coating roll substrate, so that the fresh substrate is exposed, which is more conducive to improving the adhesion between the subsequent wear-resistant coating and the coating roll substrate, and improves the coating roll Strength and hardness. Controlling the roughness after roughening not only helps to ensure the bonding force bet
Embodiment 1
[0042] This embodiment provides a coating roller, which includes a coating roller base and a composite coating, and the composite coating includes a wear-resistant coating and a low-reflection coating sequentially arranged on the surface of the coating roller base.
[0043] Wherein, the thickness of the wear-resistant coating is 0.25 mm, and the wear-resistant coating is a coating prepared from tungsten carbide powder containing only cobalt, and the mass percentage of cobalt in the tungsten carbide powder is 12%. The low-reflection coating is a coating formed from Mobil 1130 commercial mineral motor oil.
[0044] And the surface of the coating roll substrate is also provided with continuous diagonal lines, see figure 1 .
[0045] A tensile strength tester and a microhardness tester were used to test the hardness and bonding strength of the coating roll. The bonding strength of the coating roll was 75Mpa and the hardness HV0.3 was 1251.
[0046] This embodiment also provides the applicati
Embodiment 2
[0053] This embodiment provides a coating roller, the coating roller includes a coating roller base and a composite coating, and the review coating includes a wear-resistant coating and a low-reflection coating sequentially disposed on the surface of the coating roller base.
[0054] Wherein, the thickness of the wear-resistant coating is 0.15 mm, the wear-resistant coating is a coating prepared from tungsten carbide powder containing only cobalt, and the mass percentage of cobalt in the tungsten carbide powder is 10%. The low-reflection coating is a coating formed from Mobil 1130 commercial non-mineral motor oil.
[0055] And the surface of the coating roll substrate is also provided with continuous diagonal lines, see image 3 .
[0056] The bonding strength tester and the microhardness tester were used to test the hardness and bonding strength of the coating roller. The bonding strength of the coating roller was 72Mpa and the hardness HV0.3 was 1310.
[0057] This embodiment also pro
PUM
Property | Measurement | Unit |
---|---|---|
Thickness | aaaaa | aaaaa |
Roughness | aaaaa | aaaaa |
Thickness | aaaaa | aaaaa |
Abstract
Description
Claims
Application Information
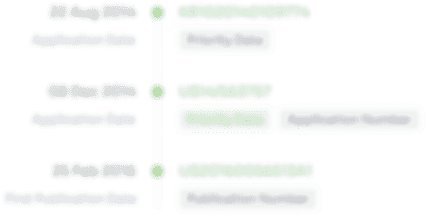
- R&D Engineer
- R&D Manager
- IP Professional
- Industry Leading Data Capabilities
- Powerful AI technology
- Patent DNA Extraction
Browse by: Latest US Patents, China's latest patents, Technical Efficacy Thesaurus, Application Domain, Technology Topic.
© 2024 PatSnap. All rights reserved.Legal|Privacy policy|Modern Slavery Act Transparency Statement|Sitemap