A core-shell structure fe 2 o 3 Preparation of @ppy composites and their application in supercapacitors
A composite material and core-shell structure technology, applied in hybrid capacitor electrodes, hybrid/electric double layer capacitor manufacturing, manganese oxide/manganese hydroxide, etc., can solve the problems of poor conductivity, poor capacity and rate performance, and achieve uniform size , reduce contact resistance, low cost effect
- Summary
- Abstract
- Description
- Claims
- Application Information
AI Technical Summary
Problems solved by technology
Method used
Image
Examples
Example Embodiment
[0047] According to the present invention, Fe 2 O 3 Preparation @PPy said composite material and its use in a supercapacitor, comprising the steps of:
[0048] (1) ZnO nano rod array prepared: foam nickel substrate, a foamed nickel was immersed in potassium permanganate solution for surface treatment, and then zinc nitrate hexahydrate zinc source, a solvent under hot alkaline solution method, foamed nickel directly grown on ZnO nano-arrays.
[0049] (2) MnO 2 Preparation nanotube array: in step (1) ZnO nanoarrays prepared containing potassium permanganate solution into the reaction vessel and sealed. 180 [deg.] C The reaction 6-12 h ~ 120. After completion of the reaction, the sample was taken out and dried. The sample was then immersed in KOH solution 1 ~ 4h, samples were removed and dried to give MnO 2 Nanotube array.
[0050] (3) Fe 2 O 3 Preparation nanotube array: ferrous sulfate heptahydrate was dissolved in a mixed solution of water and ethylene glycol and, after stirring, the
Example Embodiment
[0058] Example 1:
[0059] Preparation (1) ZnO nanorod arrays: A foamed nickel substrate, the nickel foam was immersed in a clean 0.5mol / L potassium permanganate solution for 30min surface treatment. The 1.2mmol zinc nitrate hexahydrate, 1.2mmol hexamethylene tetramine and 3ml of aqueous ammonia were added to 80mL of deionized water and stirred for 30min, then the solution was transferred to a 100mL reactor. Taken into foamed nickel autoclave, and the autoclave was sealed, for 24h at 90 ℃. After completion of the reaction, samples were taken, and dried to obtain an array of nano ZnO grown directly on a nickel foam. Micro-morphology figure 1 , The uniform nanorods grown on the nickel foam.
[0060] (2) MnO 2 Preparation nanotube array: in step (1) ZnO prepared nano-arrays placed reactor containing 0.3mol / L potassium permanganate solution, and sealed. The reaction at 180 ℃ 12 hours. After completion of the reaction, the sample was taken out and dried. The sample was then immers
Example Embodiment
[0064] Example 2:
[0065] As described in Example 1, except that: in step (4) in the B solution was slowly added dropwise to the solution A, was stirred for 30min. like Image 6 Shown, prepared in Example 2 was Fe 2 O 3 @PPy nanotube array, at 1mA / cm -2 At a current density, the area ratio of capacitance 330mF / cm -2 .
PUM
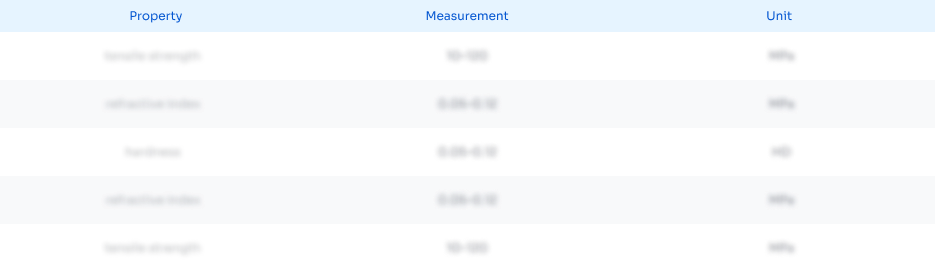
Abstract
Description
Claims
Application Information
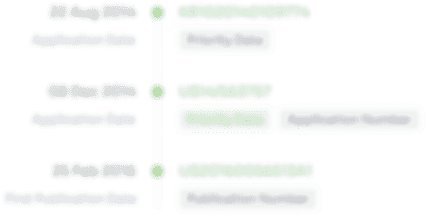
- R&D Engineer
- R&D Manager
- IP Professional
- Industry Leading Data Capabilities
- Powerful AI technology
- Patent DNA Extraction
Browse by: Latest US Patents, China's latest patents, Technical Efficacy Thesaurus, Application Domain, Technology Topic.
© 2024 PatSnap. All rights reserved.Legal|Privacy policy|Modern Slavery Act Transparency Statement|Sitemap