Process method for preparing lithium battery diaphragm by using 3D printing technology
A lithium battery diaphragm, 3D printing technology, applied in the field of lithium-ion batteries, can solve the problems of easy peeling off of the coating, complicated process, and uneven pores
- Summary
- Abstract
- Description
- Claims
- Application Information
AI Technical Summary
Problems solved by technology
Method used
Image
Examples
Embodiment 1
[0041] Step 1, mix the PP diaphragm base material, ultrafine alumina powder, and PVDF in the mixer according to the ratio of 7:2:1, transfer the evenly mixed material to the drum dry grinder, and grind to Mixed material powder with a particle size of 30 μm.
[0042] Step 2, transfer the mixed material powder obtained in step 1 to a heater with stirring, heat to 180°C to melt the material, then add NMP to adjust the viscosity of the material to 80000mPa.s, so that the material has a certain fluidity, and fully stir for 3 hours . Get the materials to be printed.
[0043] Step 3, transfer the melted material to be printed to the material injector of the 3D printer, and the nozzle arrangement width of the 3D printer is 1.5m.
[0044] The thickness of the diaphragm, the shape and diameter of the channel, the diameter of the membrane line, and the printing speed are set through the computer of the printer. After starting the printing, push the plunger of the syringe so that the mate
Embodiment 2
[0046] Step 1, mix the PE diaphragm base material, ultrafine alumina powder, and PVDF in the mixer according to the ratio of 7:2:1, transfer the evenly mixed material to the drum dry grinder, and grind to Mixed material powder with a particle size of 30 μm.
[0047] Step 2, transfer the mixed material powder obtained in step 1 to a heater with stirring, heat to 175°C to melt the material, then add NMP to adjust the viscosity of the material to 80000mPa.s, so that the material has a certain fluidity, and fully stir for 3 hours . Get the materials to be printed.
[0048] Step 3, transfer the melted material to be printed to the material injector of the 3D printer, and the nozzle arrangement width of the 3D printer is 1.5m.
[0049] The thickness of the diaphragm, the shape and diameter of the channel, the diameter of the membrane line, and the printing speed are set through the computer of the printer. After starting the printing, push the plunger of the syringe so that the mate
Embodiment 3
[0051] Step 1. Mix polypropylene non-woven diaphragm base material, ultrafine alumina powder, and PVDF in a mixer in a ratio of 7:2:1, and transfer the evenly mixed material to a drum-type dry grinder , grind to a mixed material powder with a particle size of 30 μm.
[0052] Step 2, transfer the mixed material powder obtained in step 1 to a heater with stirring, heat to 175°C to melt the material, then add NMP to adjust the viscosity of the material to 80000mPa.s, so that the material has a certain fluidity, and fully stir for 3 hours . Get the materials to be printed.
[0053] Step 3, transfer the melted material to be printed to the material injector of the 3D printer, and the nozzle arrangement width of the 3D printer is 1.5m.
[0054] The thickness of the diaphragm, the shape and diameter of the channel, the diameter of the membrane line, and the printing speed are set through the computer of the printer. After starting the printing, push the plunger of the syringe so that
PUM
Property | Measurement | Unit |
---|---|---|
Granularity | aaaaa | aaaaa |
Thickness | aaaaa | aaaaa |
Aperture | aaaaa | aaaaa |
Abstract
Description
Claims
Application Information
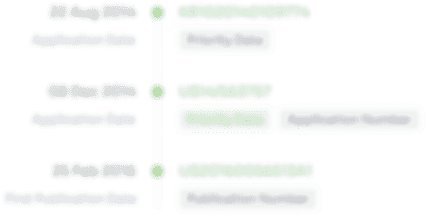
- R&D Engineer
- R&D Manager
- IP Professional
- Industry Leading Data Capabilities
- Powerful AI technology
- Patent DNA Extraction
Browse by: Latest US Patents, China's latest patents, Technical Efficacy Thesaurus, Application Domain, Technology Topic.
© 2024 PatSnap. All rights reserved.Legal|Privacy policy|Modern Slavery Act Transparency Statement|Sitemap