Method for modifying light absorption layer
a technology of light absorption layer and light absorption layer, which is applied in the direction of solid-state diffusion coating, coating, vacuum evaporation coating, etc., can solve the problems of high toxicity and pollution, high cost of hydrogen sulfide (hsub>2/sub>s) gas, and high fabrication cos
- Summary
- Abstract
- Description
- Claims
- Application Information
AI Technical Summary
Benefits of technology
Problems solved by technology
Method used
Examples
example
Example 1
[0031]The molybdenum (Mo) was coated on a soda-lime glass (SLG) substrate by a sputter method. Then, the Mo / SLG substrate was placed in a vapor deposition chamber, and the copper (Cu), indium (In), gallium (Ga) and selenium (Se) elements were deposited on the Mo / SLG substrate by a heating system to form a CIGS precursor film.
[0032]Then, the slurry containing sulfur (S) element was coated on the CIGS precursor film by a capillary coating method. The CIGS precursor film was placed on a heater plate and the slurry was dipped on it. Then, a glass cover plate was put above the CIGS precursor film. The heater was heated to about 115.2° C. (higher than the melting point of sulfur (S)), and thus the slurry containing sulfur (S) element was uniformly distributed on the CIGS precursor film by capillary force and the solvent in the slurry was removed by the heater.
[0033]Then, after the CIGS precursor film was placed and a temperature thereof was at room temperature, the glass cover wa...
example 2
[0034]The CdS (as buffer layer), iZnO / AZO (as transparent conducting layer) and top electrode were sequential formed on the light absorption layer to form a solar cell. The solar cell was divided into six smaller solar cells (Cell 1-Cell 6). Table 1 shows that photoelectric efficiency test of the six solar cells.
[0035]Table 1 shows the open-circuit voltage (Voc), short-circuit current (Jsc), fill factor, photoelectric conversion efficiency (%), series resistance (Rs) and shunt resistance (Rsh) of Example 1. The open-circuit voltage (Voc) was about 0.56-0.59 V, the short-circuit current (Jsc) was about 20-24 mA / cm2, the fill factor was about 67-69, and the photoelectric conversion efficiency (%) of the Example 1 was about 8-9.2%.
TABLE 1photoelectricVocJscF.F.conversionRshRs(V)(mA / cm2) (%)efficiency (%)(Ohm)(Ohm)Cell 10.5820.492698.242359511Cell 20.5822.274698.910214710Cell 30.5920.382698.396434611Cell 40.5621.839678.309156010Cell 50.5723.774689.189158810Cell 60.5821.542698.596243011
example 3
[0039]The fabrication method of Example 3 was the same as that of Example 2, except that the thermal process of Example 3 was conducted under 1 torr pressure. Table 3 shows the open-circuit voltage (Voc), short-circuit current (Jsc), fill factor, photoelectric conversion efficiency (%), series resistance (Rs) and shunt resistance (Rsh) of Example 3.
PUM
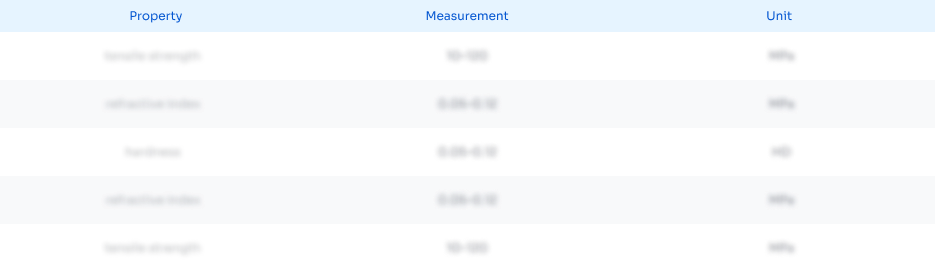
Abstract
Description
Claims
Application Information
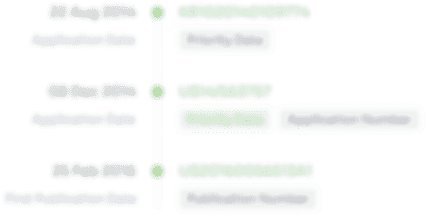
- R&D Engineer
- R&D Manager
- IP Professional
- Industry Leading Data Capabilities
- Powerful AI technology
- Patent DNA Extraction
Browse by: Latest US Patents, China's latest patents, Technical Efficacy Thesaurus, Application Domain, Technology Topic.
© 2024 PatSnap. All rights reserved.Legal|Privacy policy|Modern Slavery Act Transparency Statement|Sitemap