Coated dental powders
a dental powder and coating technology, applied in the field of coating dental powders, can solve the problems of affecting the desired geometry, affecting the processing speed of dental powder, and the optimal jointing process between dental powder and substrate is not achieved in the finished product, so as to achieve optimal shrinkage reactions of dental powders, improve processing speed, and ensure the effect of processing speed
- Summary
- Abstract
- Description
- Claims
- Application Information
AI Technical Summary
Benefits of technology
Problems solved by technology
Method used
Examples
exemplary embodiment 2
[0059 shows details of the burning-out process.
EXEMPLARY EMBODIMENT
[0060]As a starting material, 1 kg of the same leucite-apatite glass ceramic powder as in example 1 was used.
[0061]This powder was coated with a solution of the content of 1.0 mass % of PEG 1000. For coating, the GLATT fluidized bed granulator GPC G1.1 (manufacturer Glatt, Switzerland) is used.
[0062]The powder is filled into the funnel of the Glatt unit and the tube of the conveyor pump is immersed in the PEG solution.
[0063]The parameters had to be adjusted, but are adjusted during the coating process. Care was to be taken that the amount of liquid and feed air temperature were adjusted such that the powder did not form lumps.
Experimental Parameters:
[0064]
Feed air temp.:35-40° C.Spray pressure:1 barPump position:30-35%Amount sprayed:about 14.2 ml / minAmount of air:80-120 m3 / hTime of coating:70.5 minDrying time:until a product temperature of 24° C. isreached
[0065]In the result of this experiment, t...
PUM
Property | Measurement | Unit |
---|---|---|
temperatures | aaaaa | aaaaa |
temperatures | aaaaa | aaaaa |
time | aaaaa | aaaaa |
Abstract
Description
Claims
Application Information
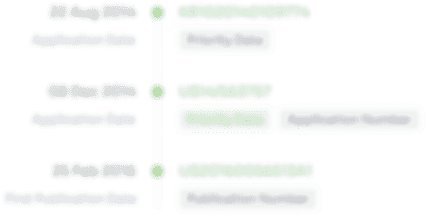
- R&D Engineer
- R&D Manager
- IP Professional
- Industry Leading Data Capabilities
- Powerful AI technology
- Patent DNA Extraction
Browse by: Latest US Patents, China's latest patents, Technical Efficacy Thesaurus, Application Domain, Technology Topic.
© 2024 PatSnap. All rights reserved.Legal|Privacy policy|Modern Slavery Act Transparency Statement|Sitemap