Preparation method of superfine fiber high-imitation grain synthetic leather
一种仿头层皮、超细纤维的技术,应用在纤维处理、化学仪器和方法、合成树脂层状产品等方向,能够解决无法取代头层皮、没有天然头层皮手感表面效果、无法达到头层皮价位等问题,达到提升国际竞争力、泡孔大小和分布均匀、提高品质的效果
- Summary
- Abstract
- Description
- Claims
- Application Information
AI Technical Summary
Problems solved by technology
Method used
Examples
Embodiment 1
[0029] (1) Spinning of composite fibers
[0030] Nylon 6 slices and low-density polyethylene are mixed according to the mass ratio of 50:50, extruded and melted by a screw extruder, and the spinning temperature range is controlled at 245-285°C, after cooling and blowing (air temperature 25°C), pulling Stretching (drawing ratio 4.5 times), oiling (oil concentration 4.0%), crimping (the number of crimps is 20 / 25mm) and cutting, spinning 6D×51mm sea-island composite fibers, nylon 6 in the composite fibers For the island component, low density polyethylene is for the sea component.
[0031] (2) Production of non-woven fabrics
[0032] Use the island-in-the-sea composite fiber prepared in step (1) to make a non-woven fabric with a width of 1.55m and a thickness of 1.50-1.70mm. Its density reaches 0.29g / cm 3 , The thickness reaches 1.48mm. The process parameters of non-woven fabric production are needle punching frequency 500-1000 punches / min, needle punching density 1000-1500 p...
Embodiment 2
[0043] (1) Spinning of composite fibers
[0044] Nylon 6 slices and low-density polyethylene are mixed according to the mass ratio of 55:45, extruded and melted by a screw extruder, and the spinning temperature range is controlled at 245-285°C, and cooled and blown (air temperature 20°C) , drafting (drawing ratio 4 times), oiling (oil concentration 6.0%), crimping (17 crimps / 25mm) and cutting, and spinning a 7D×38mm sea-island composite fiber. Nylon 6 is the island component, and low-density polyethylene is the sea component.
[0045] (2) Production of non-woven fabrics
[0046] Use the island-in-the-sea composite fiber prepared in step (1) to make a non-woven fabric with a width of 1.65m and a thickness of 1.95-2.15mm. Its density reaches 0.30g / cm 3 , The thickness reaches 1.75mm. The process parameters of non-woven fabric production are needle punching frequency 1000-1500 punches / min, needle punching density 1500-2000 punches / m 2 , The number of laying layers is 40 laye...
Embodiment 3
[0057] (1) Spinning of composite fibers
[0058] Nylon 6 slices and low-density polyethylene are mixed according to the mass ratio of 60:40, extruded and melted by a screw extruder, and the spinning temperature range is controlled at 245-285°C, and cooled and blown (air temperature 16°C) , drafting (drawing ratio 6 times), oiling (oil concentration 10%), crimping (the number of crimps is 22 / 25mm) and cutting, and spinning a sea-island composite fiber of 5D×64mm, the composite fiber Nylon 6 is the island component, and low-density polyethylene is the sea component.
[0059] (2) Production of non-woven fabrics
[0060] Use the island-in-the-sea composite fiber prepared in step (1) to make a non-woven fabric with a width of 1.70m and a thickness of 3.10-3.30mm. Its density reaches 0.28g / cm 3 , The thickness reaches 3.0mm. The process parameters of non-woven fabric production are acupuncture frequency 800-1200 punches / min, acupuncture density 900-1700 punches / m 2 , The number...
PUM
Property | Measurement | Unit |
---|---|---|
solid containing ratio | aaaaa | aaaaa |
solid containing ratio | aaaaa | aaaaa |
base weight | aaaaa | aaaaa |
Abstract
Description
Claims
Application Information
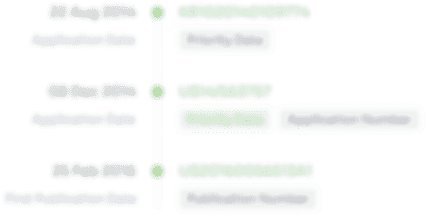
- R&D Engineer
- R&D Manager
- IP Professional
- Industry Leading Data Capabilities
- Powerful AI technology
- Patent DNA Extraction
Browse by: Latest US Patents, China's latest patents, Technical Efficacy Thesaurus, Application Domain, Technology Topic.
© 2024 PatSnap. All rights reserved.Legal|Privacy policy|Modern Slavery Act Transparency Statement|Sitemap