Method for preparing cobalt-based wear-resistant and corrosion-resistant coating layer by adopting ultra-high speed laser cladding
一种激光熔覆、速率的技术,应用在涂层、金属材料涂层工艺等方向,能够解决成本高、效率低下等问题,达到变形量小、提高生产效率、降低生产成本的效果
- Summary
- Abstract
- Description
- Claims
- Application Information
AI Technical Summary
Problems solved by technology
Method used
Examples
Embodiment 1
[0028] The invention provides a method for preparing a cobalt-based wear-resistant and corrosion-resistant coating by ultra-high-speed laser cladding. Preferably, the steps of the method include:
[0029] (1) Sieve and purify the cobalt-based alloy powder, dry it and store it in vacuum for later use;
[0030] (2) Set the process parameters of ultra-high-speed laser cladding;
[0031] (3) Clamp the substrate with a smooth surface and no defects on the rotary mechanism of the numerical control equipment, and adjust the positions of the light spot (laser focus) and powder spot (cobalt-based alloy powder convergence point) relative to the substrate to be clad, so that the cobalt-based More than 80% of the energy of the laser beam acts on the powder material;
[0032] (4) Using the coaxial powder feeding ultra-high-speed laser cladding method, the cobalt-based alloy powder obtained in step (1) is clad on the surface of the substrate to obtain a cobalt-based wear-resistant and cor...
Embodiment 2
[0041] Provided is a method for preparing a cobalt-based wear-resistant and corrosion-resistant coating on the surface of a nuclear power seawater pump shaft by ultra-high-speed laser cladding. To be less than 0.4mm in diameter of the finished product, and then use the ultra-high-speed laser cladding method of coaxial powder feeding to clad the cobalt-based coating on the surface of the substrate, and then use the laser remelting method to melt the incompletely melted powder on the coating surface to ensure the coating surface roughness. Its specific process steps are:
[0042] (1) Sieve and purify the cobalt-based alloy powder to obtain a powder with a particle size range of 15-45 μm and a sphericity greater than 90%, and then dry it at a holding temperature of 130°C for a holding time of 2 hours, then vacuum seal it for future use;
[0043](2) Set the process parameters of ultra-high-speed laser cladding. The specific process is: the diameter of the spot is 1.2mm, the linea...
PUM
Property | Measurement | Unit |
---|---|---|
particle diameter | aaaaa | aaaaa |
spheroidization ratio | aaaaa | aaaaa |
diameter | aaaaa | aaaaa |
Abstract
Description
Claims
Application Information
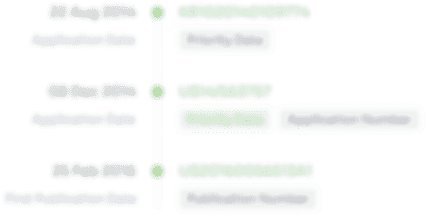
- R&D Engineer
- R&D Manager
- IP Professional
- Industry Leading Data Capabilities
- Powerful AI technology
- Patent DNA Extraction
Browse by: Latest US Patents, China's latest patents, Technical Efficacy Thesaurus, Application Domain, Technology Topic.
© 2024 PatSnap. All rights reserved.Legal|Privacy policy|Modern Slavery Act Transparency Statement|Sitemap