Refractory ceramic tile and preparation method thereof
A ceramic brick and refractory technology, applied in the field of refractory materials, can solve problems such as poor mechanical properties, achieve high yield, good compatibility, and broad market prospects
- Summary
- Abstract
- Description
- Claims
- Application Information
AI Technical Summary
Benefits of technology
Problems solved by technology
Method used
Examples
Embodiment 1
[0031] This embodiment relates to a refractory ceramic brick, including the following raw materials in parts by weight: 10 parts of modified asbestos powder, 15 parts of corundum sand, 7 parts of dolomite, 14 parts of perlite, 10 parts of modified quartz powder, 20 parts of bentonite, 15 parts of montmorillonite powder, 3 parts of mullite fiber, 4 parts of magnesium oxide, 2 parts of zirconium dioxide, 3 parts of nano aluminum hydroxide, and 4 parts of binder.
[0032] Wherein, the preparation method of described modified asbestos powder is as follows:
[0033] Add bamboo carbon powder equivalent to 0.5% of the weight of asbestos powder, 0.4% epoxy linseed oil, 0.2% silane coupling agent KH792 and an appropriate amount of deionized water to the asbestos powder, and stir at 300r / min at 40-45 After stirring and reacting at ℃ for 20 minutes, take it out and dry it to obtain modified asbestos powder.
[0034] Wherein, the preparation method of described modified quartz powder is a
Embodiment 2
[0050]This embodiment relates to a refractory ceramic brick, including the following raw materials in parts by weight: 20 parts of modified asbestos powder, 25 parts of corundum sand, 13 parts of dolomite, 21 parts of perlite, 18 parts of modified quartz powder, 30 parts of bentonite, 25 parts of montmorillonite powder, 6 parts of mullite fiber, 9 parts of magnesium oxide, 4 parts of zirconium dioxide, 6 parts of nano aluminum hydroxide, and 7 parts of binder.
[0051] Wherein, the preparation method of described modified asbestos powder is as follows:
[0052] Add bamboo carbon powder equivalent to 0.5% of the weight of asbestos powder, 0.4% epoxy linseed oil, 0.2% silane coupling agent KH792 and an appropriate amount of deionized water to the asbestos powder, and stir at 300r / min at 40-45 After stirring and reacting at ℃ for 20 minutes, take it out and dry it to obtain modified asbestos powder.
[0053] Wherein, the preparation method of described modified quartz powder is a
Embodiment 3
[0069] This embodiment relates to a refractory ceramic brick, including the following raw materials in parts by weight: 13 parts of modified asbestos powder, 18 parts of corundum sand, 10 parts of dolomite, 15 parts of perlite, 14 parts of modified quartz powder, 22 parts of bentonite, 17 parts of montmorillonite powder, 4 parts of mullite fiber, 5 parts of magnesium oxide, 2.5 parts of zirconium dioxide, 4 parts of nano aluminum hydroxide, and 5 parts of binder.
[0070] Wherein, the preparation method of described modified asbestos powder is as follows:
[0071] Add bamboo carbon powder equivalent to 0.5% of the weight of asbestos powder, 0.4% epoxy linseed oil, 0.2% silane coupling agent KH792 and an appropriate amount of deionized water to the asbestos powder, and stir at 300r / min at 40-45 After stirring and reacting at ℃ for 20 minutes, take it out and dry it to obtain modified asbestos powder.
[0072] Wherein, the preparation method of described modified quartz powder i
PUM
Property | Measurement | Unit |
---|---|---|
Particle size | aaaaa | aaaaa |
Particle size | aaaaa | aaaaa |
Particle size | aaaaa | aaaaa |
Abstract
Description
Claims
Application Information
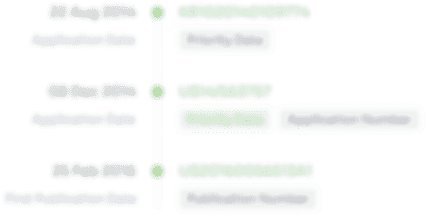
- R&D Engineer
- R&D Manager
- IP Professional
- Industry Leading Data Capabilities
- Powerful AI technology
- Patent DNA Extraction
Browse by: Latest US Patents, China's latest patents, Technical Efficacy Thesaurus, Application Domain, Technology Topic.
© 2024 PatSnap. All rights reserved.Legal|Privacy policy|Modern Slavery Act Transparency Statement|Sitemap