High-strength TPU composite thermal insulation fabric and preparation method thereof
A high-strength, fabric technology, applied in the field of textile fabrics, can solve the problems of thermal insulation and moisture permeability, decreased mechanical properties of materials, poor bonding strength, etc., to improve bond strength and mechanical properties, reduce thermal conductivity, improve structure performance effect
- Summary
- Abstract
- Description
- Claims
- Application Information
AI Technical Summary
Problems solved by technology
Method used
Examples
Example Embodiment
[0028] Example 1
[0029] Take coconut shells and place them at room temperature to dry naturally, collect and pulverize dry coconut shells, collect pulverized particles and weigh 45 parts by weight of 3% hydrogen peroxide, 3 parts of pulverized particles and 1 A portion of glacial acetic acid was placed in a beaker, stirred and mixed, and placed in a water bath at 85°C for 3 hours of heating treatment, and allowed to cool to room temperature. Process fiber; take kapok fiber and weigh 45-50 parts of deionized water, 3 parts of sodium sulfite, 1 part of sodium silicate, 0.5 part of sodium silicate, 3 parts of sodium hydroxide, 1 part of fatty alcohol by weight. Polyoxyethylene ether and 10 parts of kapok fibers were placed in a beaker, stirred and mixed and placed in an oil bath for 100 min at 90 °C, then centrifuged at 1500 r / min to collect the next precipitate, rinsed with deionized water until the washing solution Neutral to obtain alkali-treated kapok fibers, weigh 68 parts
Example Embodiment
[0030] Example 2
[0031] Take coconut shells and place them at room temperature to dry naturally, collect and pulverize dry coconut shells, collect pulverized particles and weigh 47 parts by weight of 3% hydrogen peroxide, 4 parts of pulverized particles and 1 A portion of glacial acetic acid was placed in a beaker, stirred and mixed and placed in a water bath at 87°C for 4 hours of heating treatment, left to cool to room temperature, filtered and collected the filter cake, washed with deionized water until the filter cake was neutral, and the degummed solution was obtained. Process fibers; take kapok fibers and weigh 47 parts of deionized water, 4 parts of sodium sulfite, 1 part of sodium silicate, 0.7 parts of sodium silicate, 4 parts of sodium hydroxide, 1 part of fatty alcohol polyoxy Vinyl ether and 12 parts of kapok fibers were placed in a beaker, stirred and mixed, and placed in an oil bath for 110 min at 95°C, then centrifuged at 1750 r / min to collect the next precipit
Example Embodiment
[0032] Example 3
[0033] Take coconut shells and place them at room temperature to dry naturally, collect and pulverize dry coconut shells, collect pulverized particles and weigh 50 parts by weight of 3% hydrogen peroxide, 5 parts of pulverized particles and 2 parts by weight. A portion of glacial acetic acid was placed in a beaker, stirred and mixed and placed in a water bath at 90°C for 5 hours of heating treatment, left to cool to room temperature, filtered and collected the filter cake, washed with deionized water until the filter cake was neutral, and the degummed solution was obtained. Process fiber; take kapok fiber and weigh 50 parts of deionized water, 5 parts of sodium sulfite, 2 parts of sodium silicate, 1.0 parts of sodium silicate, 5 parts of sodium hydroxide, 2 parts of fatty alcohol polyoxy Vinyl ether and 15 parts of kapok fibers were placed in a beaker, stirred and mixed and placed in an oil bath for 120 min at 100 °C, then centrifuged at 2000 r / min to collect
PUM
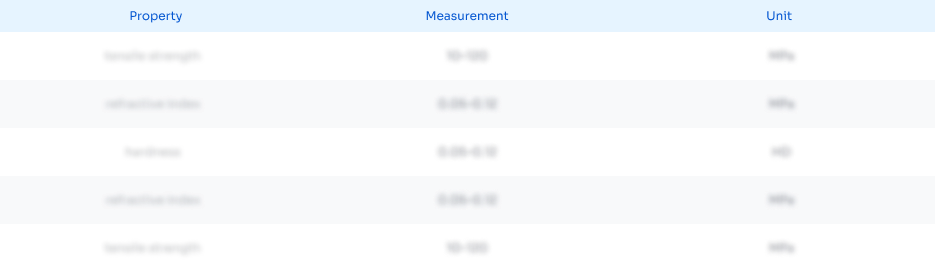
Abstract
Description
Claims
Application Information
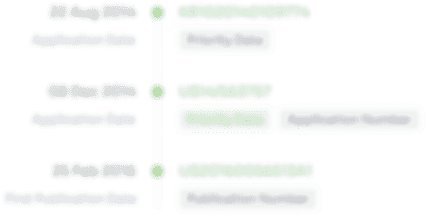
- R&D Engineer
- R&D Manager
- IP Professional
- Industry Leading Data Capabilities
- Powerful AI technology
- Patent DNA Extraction
Browse by: Latest US Patents, China's latest patents, Technical Efficacy Thesaurus, Application Domain, Technology Topic.
© 2024 PatSnap. All rights reserved.Legal|Privacy policy|Modern Slavery Act Transparency Statement|Sitemap