Polyurethane cable insulating material and preparation method thereof
A cable insulation, polyurethane technology, applied in insulators, organic insulators, plastic/resin/wax insulators, etc., can solve the problems of acid and alkali resistance, poor oil resistance, difficult production process, poor tear resistance, etc., to achieve tear strength. High, simple processing technology, high production efficiency
- Summary
- Abstract
- Description
- Claims
- Application Information
AI Technical Summary
Benefits of technology
Problems solved by technology
Method used
Image
Examples
Embodiment 1
[0022] A polyurethane cable insulation material, which is made of component A and component B according to the following parts by weight:
[0023] A component:
[0024]
[0025] B component:
[0026] The mixture of PM200, MDI50 and TDI with a mass ratio of 2:7:3 and the polyether polyol with a functionality of 2 and a molecular weight of 700 were reacted at 80±5°C for 3 hours according to a mass ratio of 3.5:1 to obtain an NCO% of 150 parts of 26% modified black material.
[0027] When preparing, add the raw materials of component A into the mixer and mix evenly, adjust the constant temperature of the material to 25±2°C, adjust the speed of the mixer to 4000r / min (using this range of speed can more fully mix the materials of each component), Pour component B preheated to 25±2°C into component A and stir for 5 seconds, pour the mixture into the mold, and mature for 24 hours to obtain the product.
Embodiment 2
[0029] A polyurethane cable insulation material, which is made of component A and component B according to the following parts by weight:
[0030] A component:
[0031]
[0032] B component:
[0033] The mixture of PM200, MDI50 and TDI with a mass ratio of 2:7:3 and the polyether polyol with a functionality of 2 and a molecular weight of 700 were reacted at 80±5°C for 2 hours according to a mass ratio of 3.5:1 to obtain NCO% of 65 parts of 26% modified black material.
[0034] When preparing, add the raw materials of component A into the mixer and mix evenly, adjust the constant material temperature to 25±2°C, and adjust the speed of the agitator to 4000r / min (using this range of speed can more fully mix the materials of each component), Pour component B preheated to 25±2°C into component A and stir for 5 seconds, pour the mixture into the mold, and mature for 24 hours to obtain the product.
Embodiment 3
[0036] A polyurethane cable insulation material, which is made of component A and component B according to the following parts by weight:
[0037] A component:
[0038]
[0039]
[0040] B component:
[0041] The mixture of PM200, MDI50, and TDI with a mass ratio of 2:7:3 and the polyether polyol with a functionality of 2 and a molecular weight of 700 were reacted at 80±5°C for 2.5 hours at a mass ratio of 3.5:1 to obtain an NCO% of 110 parts of 26% modified black material.
[0042] When preparing, add the raw materials of component A into the mixer and mix evenly, adjust the constant material temperature to 25±2°C, and adjust the speed of the agitator to 4000r / min (using this range of speed can more fully mix the materials of each component), Pour component B preheated to 25±2°C into component A and stir for 5 seconds, pour the mixture into the mold, and mature for 24 hours to obtain the product.
[0043] The performance test is as follows:
[0044] Tensil
PUM
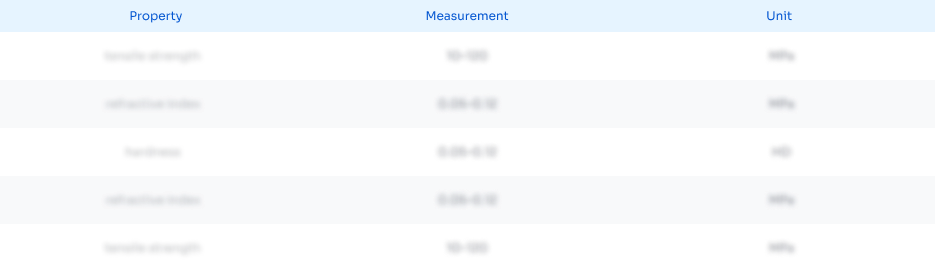
Abstract
Description
Claims
Application Information
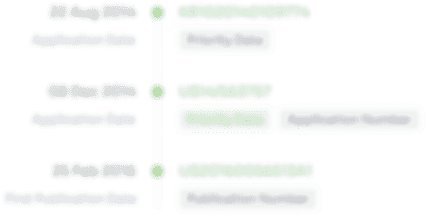
- R&D Engineer
- R&D Manager
- IP Professional
- Industry Leading Data Capabilities
- Powerful AI technology
- Patent DNA Extraction
Browse by: Latest US Patents, China's latest patents, Technical Efficacy Thesaurus, Application Domain, Technology Topic.
© 2024 PatSnap. All rights reserved.Legal|Privacy policy|Modern Slavery Act Transparency Statement|Sitemap