Shading polypropylene base film for photographic paper and preparation method of shading polypropylene base film
一种聚丙烯基膜、聚丙烯树脂的技术,应用在化学仪器和方法、应用、家里用具等方向,能够解决降低相纸基膜透光率、遮光性不良等问题,达到有利于水汽透过率、水汽透过率低、防止球晶形成的效果
- Summary
- Abstract
- Description
- Claims
- Application Information
AI Technical Summary
Problems solved by technology
Method used
Examples
Embodiment 1
[0048] Preparation of core layer polypropylene composition: get 60 parts of polypropylene HE425H resin, 20 parts of titanium dioxide, 1 part of silane coupling agent (KH-550), 0.1 part / 0.2 part of antioxidant (1010 / 168), carbon black (SP5000 ) 0.1 part, 0.1 part of dispersant ethylene bis stearamide is granulated in a co-rotating twin-screw extruder with an aspect ratio of 32:1, the granulation temperature is 180 ° C, the main engine speed is 400 rpm / min, and the feeding speed is 25r / min to prepare the core layer polypropylene composition.
[0049] Preparation of surface layer polypropylene composition: 60 parts of polypropylene HJ730 resin, 3 parts of antistatic agent (rgastat P16), and 0.1 part of dispersant ethylene bisstearamide were pelletized in a co-rotating twin-screw extruder to obtain Surface layer polypropylene composition.
Embodiment 2
[0051] Preparation of core layer polypropylene composition: take 60 parts of polypropylene HE425H resin, 20 parts of titanium dioxide, 5 parts of talcum powder, 1 part of silane coupling agent (KH-550), 0.1 part / 0.2 part of antioxidant (1010 / 168) , 0.1 part of carbon black (SP5000), 0.1 part of dispersant ethylene bis stearamide was granulated in a co-rotating twin-screw extruder with an aspect ratio of 32:1, the granulation temperature was 185°C, and the speed of the main machine was 420rpm / min , the feeding speed is 28r / min, and the core layer polypropylene composition is prepared.
[0052] Prepare the surface layer polypropylene composition: granulate 60 parts of polypropylene HJ730 resin, 3 parts of antistatic agent (rgastat P18), and 0.1 part of dispersant ethylene bisstearamide in a co-rotating twin-screw extruder to obtain the surface layer Polypropylene composition.
Embodiment 3
[0054] Preparation of core layer polypropylene composition: get 60 parts of polypropylene T350 resin, 30 parts of kaolin, 1 part of silane coupling agent (KH-570), 0.1 part / 0.2 part of antioxidant (1010 / 168), carbon black (N330 ) 0.1 part, 0.1 part of dispersant ethylene bis stearamide was granulated in a co-rotating twin-screw extruder, the granulation temperature was 190°C, the main engine speed was 450rpm / min, and the feeding speed was 30r / min to obtain the core layer Polypropylene composition.
[0055] Prepare the surface layer polypropylene composition: granulate 70 parts of polypropylene HJ730 resin, 8 parts of antistatic agent (rgastat P18), and 0.1 part of dispersant ethylene bisstearamide in a co-rotating twin-screw extruder to obtain Surface layer polypropylene composition.
PUM
Property | Measurement | Unit |
---|---|---|
melt flow index | aaaaa | aaaaa |
melting point | aaaaa | aaaaa |
density | aaaaa | aaaaa |
Abstract
Description
Claims
Application Information
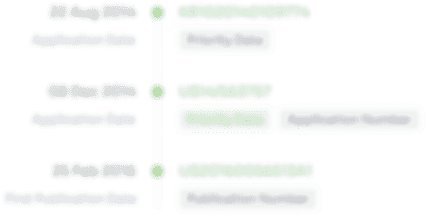
- R&D Engineer
- R&D Manager
- IP Professional
- Industry Leading Data Capabilities
- Powerful AI technology
- Patent DNA Extraction
Browse by: Latest US Patents, China's latest patents, Technical Efficacy Thesaurus, Application Domain, Technology Topic.
© 2024 PatSnap. All rights reserved.Legal|Privacy policy|Modern Slavery Act Transparency Statement|Sitemap