Activation system and method for enhancing metal recovery during atmospheric leaching of metal sulfides
a technology of metal sulfide and activation system, which is applied in the field of equipment, can solve the problems of poor metal recovery, low reaction kinetics, and unattractive large-scale commercial applications, and achieve the effect of improving the hydrometallurgical processing of primary metal sulfides and promoting rapid metal dissolution
- Summary
- Abstract
- Description
- Claims
- Application Information
AI Technical Summary
Benefits of technology
Problems solved by technology
Method used
Examples
example 1
[0056]In this Example we describe the use of a unique Physico-chemical activation process, involving the use of a shear-tank reactor 212, to enhance the oxidative leaching of chalcopyrite under atmospheric conditions to produce greater than 97% copper recoveries in under 4 hours.
[0057]Contrary to prior approaches which focused on high-yield metathesis reactions for complete conversions of chalcopyrite to other copper sulfides in order to facilitate secondary sulfide leaching, the inventors have unexpectedly discovered that low-yield metathesis reactions are much more effective and economical for leaching primary metal sulfides. These low-yield metatheses reactions may be advantageously utilized as a pre-activation process via a reductive activation circuit 220, prior to oxidative leaching in an oxidative leach circuit 240. Accordingly, it may be desirable to provide a reductive activation circuit 220 which is adequately configured to produce these low-yield metathesis products.
[0058...
example 2
[0063]In this Example we further describe the use of Physico-Chemical activation to enhance the oxidative leaching of chalcopyrite. In stage one, the chalcopyrite is treated reductively to partially convert chalcopyrite to a metastable, non-stoichiometric binary copper sulfide according to the following reaction stoichiometry:
CuxFeyS2+ZCuSO4→Cux+zFey−zS2+ZFeSO4
[0064]The reductive activation was conducted completely within a shear-tank reactor 212 at 80° C., a solids concentration of 15%, pH≈1.8, and enough copper sulfate to yield approximately 6.5% conversion of chalcopyrite. In this example, the shear-tank reactor was configured as a stirred media reactor comprising grinding media. The molar ratio of the initial solution copper to soluble iron which was contained within the concentrate feed was 0.066. The chalcopyrite concentrate, having a particle size distribution with a P80 of 17.5 μm, along with 2.5 g L−1 copper sulfate and 2 g L−1 ferrous sulfate were charged into the shear-t...
example 3
[0073]This Example illustrates the use of a Physico-Chemical activation process to enhance chalcopyrite dissolution by atmospheric, acidic ferric sulfate leaching. Test conditions were identical to Example 2, except the residence time in the shear-tank reactor 212 during Physico-Chemical activation was limited to the time it took for complete copper uptake by the chalcopyrite concentrate. The rate of copper uptake by the concentrate is shown in FIG. 3. Reduction of the soluble copper concentration to below the detection limit was complete within about 15-17 minutes. A total mixing energy for the shear-tank reactor 212 of about 20 kW·h / tonne had been expended during the activation stage. After completing the Physico-Chemical activation, the slurry was transferred to a stirred-tank reactor 202 as shown in FIG. 6, with a lixiviant composition of 20 g L−1 ferric, and 49 g L−1 H2SO4 and the copper was leached oxidatively at 80° C. The activated slurry was recirculated between the stirred...
PUM
Property | Measurement | Unit |
---|---|---|
temperatures | aaaaa | aaaaa |
residence time | aaaaa | aaaaa |
residence time | aaaaa | aaaaa |
Abstract
Description
Claims
Application Information
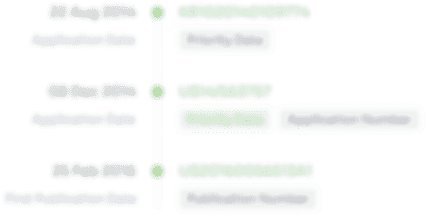
- R&D Engineer
- R&D Manager
- IP Professional
- Industry Leading Data Capabilities
- Powerful AI technology
- Patent DNA Extraction
Browse by: Latest US Patents, China's latest patents, Technical Efficacy Thesaurus, Application Domain, Technology Topic.
© 2024 PatSnap. All rights reserved.Legal|Privacy policy|Modern Slavery Act Transparency Statement|Sitemap