Method for reinforcing titanium concentrate pellet prereduction
一种钛精矿、球团的技术,应用在强化钛精矿球团预还原领域,能够解决金属化率低等问题,达到提高金属化率、改善冶炼炉况、操作方便的效果
- Summary
- Abstract
- Description
- Claims
- Application Information
AI Technical Summary
Problems solved by technology
Method used
Examples
Embodiment 1
[0040] Take by weighing 10Kg of titanium concentrate of Table 1 composition, 0.3Kg of the mixture of sodium bentonite and sodium carboxymethyl cellulose (mass ratio is 1:2), 0.4Kg of water, 2Kg of carbonized coal, and press on a roller skin briquetting machine to form The speed of the ball and roller skin briquetting machine is 6r / min, and the pressure is 16MPa. After the pressed pellets are dried, the strength of the pellets is above 1000N. Select 20 pellets of this kind and place them in a resistance furnace to oxidize for 10 minutes at a temperature of 1050°C. Coat the surface of the oxidized pellets with a layer of anthracite coal powder at 1300°C. ℃ for 30 minutes, and the reduced pellets were cooled in the furnace.
[0041] The reduction rate of pellets in this embodiment can reach about 90%.
Embodiment 2
[0043] Take by weighing 10Kg of titanium concentrate of Table 1 composition, 0.3Kg of the mixture of sodium bentonite and sodium carboxymethyl cellulose (mass ratio is 1:2), 0.4Kg of water, 2Kg of carbonized coal, and press on a roller skin briquetting machine to form The speed of the ball and roller skin briquetting machine is 6r / min, and the pressure is 16MPa. After the pressed pellets are dried, the strength of the pellets is above 1000N. Select 20 pellets of this kind and place them in a resistance furnace to oxidize for 10 minutes at a temperature of 1000°C. Coat the surface of the oxidized pellets with a layer of anthracite coal powder at 1250°C. ℃ for 25 minutes, and the reduced pellets were cooled in the furnace.
[0044] The reduction rate of pellets in this embodiment can reach about 85%.
[0045] The method provided by the invention can change the phase of the titanium concentrate, effectively improve the subsequent pre-reduction metallization rate, and the pre-red...
PUM
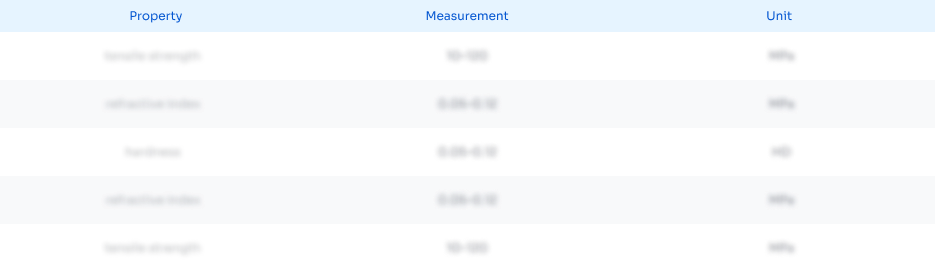
Abstract
Description
Claims
Application Information
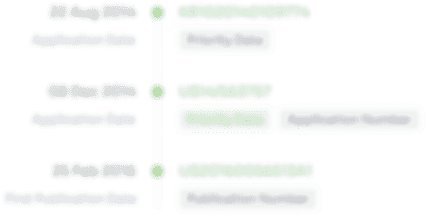
- R&D Engineer
- R&D Manager
- IP Professional
- Industry Leading Data Capabilities
- Powerful AI technology
- Patent DNA Extraction
Browse by: Latest US Patents, China's latest patents, Technical Efficacy Thesaurus, Application Domain, Technology Topic.
© 2024 PatSnap. All rights reserved.Legal|Privacy policy|Modern Slavery Act Transparency Statement|Sitemap