Preparation method of anodic oxide film
一种阳极氧化膜、阳极氧化的技术,应用在阳极氧化、电解涂料、表面反应电解涂层等方向,能够解决皮膜龟裂、气体腐蚀性高、铝基材与反应颗粒度超标等问题,达到提升耐腐蚀性能和耐电压性、提升使用寿命的效果
- Summary
- Abstract
- Description
- Claims
- Application Information
AI Technical Summary
Problems solved by technology
Method used
Examples
Embodiment 1
[0060] This embodiment provides a method for preparing an anodic oxide film, and the flow chart of the preparation method is as follows: figure 1 As shown, the preparation method comprises the following steps:
[0061] (1) Degreasing treatment: The aluminum alloy casting is immersed in 200g / L of degreasing agent, and soaked for 5 minutes at 60°C. The degreasing agent is composed of 25% sulfuric acid, 1% sodium alkyl sulfonate, and the balance is water;
[0062] (2) The first water washing treatment: repeatedly rinse the aluminum alloy casting with deionized water for 4 minutes;
[0063] (3) Alkaline etching treatment: Immerse the aluminum alloy casting into 40g / L sodium hydroxide solution, and soak it at 50°C for 2min;
[0064] (4) The second water washing treatment: repeatedly rinse the aluminum alloy casting with deionized water for 4 minutes;
[0065] (5) Neutralization treatment: immerse the aluminum alloy casting into 200g / L nitric acid solution for 15min;
[0066] (6)...
Embodiment 2
[0072] This embodiment provides a preparation method of an anodic oxide film, and the preparation method includes the following steps:
[0073] (1) Degreasing treatment: Immerse the aluminum alloy castings in 180g / L degreasing agent, soaked at 55°C for 10 min. The degreasing agent is composed of 20% sulfuric acid, 1% fatty alcohol polyoxyethylene ether, 1% alkylsulfonic acid Sodium and the balance are composed of water;
[0074] (2) The first water washing treatment: repeatedly rinse the aluminum alloy casting with deionized water for 3 minutes;
[0075] (3) Alkaline etching treatment: Immerse the aluminum alloy casting into 30g / L sodium hydroxide solution, and soak it at 45°C for 3min;
[0076] (4) The second water washing treatment: repeatedly rinse the aluminum alloy casting with deionized water for 3 minutes;
[0077] (5) Neutralization treatment: Immerse the aluminum alloy casting into 190g / L nitric acid solution for 20min;
[0078] (6) The third water washing treatmen...
Embodiment 3
[0084] This embodiment provides a preparation method of an anodic oxide film, and the preparation method includes the following steps:
[0085] (1) Degreasing treatment: Immerse the aluminum alloy castings in 220g / L degreasing agent, soaked at 65°C for 10min. The degreasing agent is composed of 30% sulfuric acid, 1.5% fatty alcohol polyoxyethylene ether, 0.3% alkylsulfonic acid Sodium and the balance are composed of water;
[0086] (2) The first water washing treatment: repeatedly rinse the aluminum alloy casting with deionized water for 5 minutes;
[0087] (3) Alkaline etching treatment: Immerse the aluminum alloy casting into 50g / L sodium hydroxide solution, and soak it at 55°C for 1min;
[0088] (4) The second water washing treatment: repeatedly rinse the aluminum alloy casting with deionized water for 3 minutes;
[0089] (5) Neutralization treatment: Immerse the aluminum alloy casting into 210g / L nitric acid solution for 10min;
[0090] (6) The third water washing treat...
PUM
Property | Measurement | Unit |
---|---|---|
current density | aaaaa | aaaaa |
Abstract
Description
Claims
Application Information
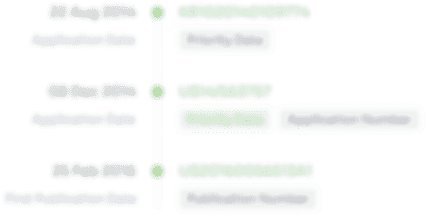
- R&D Engineer
- R&D Manager
- IP Professional
- Industry Leading Data Capabilities
- Powerful AI technology
- Patent DNA Extraction
Browse by: Latest US Patents, China's latest patents, Technical Efficacy Thesaurus, Application Domain, Technology Topic.
© 2024 PatSnap. All rights reserved.Legal|Privacy policy|Modern Slavery Act Transparency Statement|Sitemap