Method for fabricating a group III nitride semiconductor laser device
a semiconductor laser and nitride technology, applied in semiconductor lasers, laser details, nanooptics, etc., can solve the problems of unsatisfactory end surfaces, unfavorable mechanical defects, and unsatisfactory device characteristics such as working life, and achieve the effect of preventing mechanical defects
- Summary
- Abstract
- Description
- Claims
- Application Information
AI Technical Summary
Benefits of technology
Problems solved by technology
Method used
Examples
first embodiment
[0056]FIG. 3 is a vertical sectional view schematically showing the structure of the semiconductor laser device 1 of a first embodiment of the invention, and FIGS. 1 and 2 are vertical sectional views schematically showing its layer structure as observed in the middle of its fabrication. In all these figures, the dislocation-concentrated region X1 and the high-luminescence region Y1 of the substrate are also shown.
[0057] The semiconductor laser device 1 was produced in the following manner. First, on an n-type GaN substrate 100 produced as described above, a layered structure 101 was formed (FIG. 1) by forming, through successive crystal growth by MOCVD (metalorganic chemical vapor deposition), a 3 μm n-type GaN layer 102, a 40 nm n-type In0.07Ga0.93N crack prevention layer 103, a 1.2 μm n-type Al0.1Ga0.9N clad layer 104, a 0.1 μm n-type GaN optical guide layer 105, a triple quantum well active layer 106 composed of 4 nm In0.1Ga0.9N well layers and 8 nm In0.01Ga0.99N barrier layers...
second embodiment
[0070]FIG. 5 is a vertical sectional view schematically showing the structure of the semiconductor laser device 2 of a second embodiment of the invention, and FIG. 4 is a vertical sectional view schematically showing its layer structure in the middle of its fabrication. The semiconductor laser device 2 of this embodiment is a modified version of the semiconductor laser device 1 of the first embodiment in which dielectric films 115 are additionally formed, one in a portion of the top surface of the embedded layer 112 located right above the dislocation-concentrated region X1 of the n-type GaN substrate 100 and another in a portion of the bottom surface of the substrate 100 located right below the dislocation-concentrated region X1. The n-type GaN substrate 100 and the layered structure 101 are structured and produced in the same manner as in the first embodiment, and therefore overlapping explanations will not be repeated.
[0071] The dielectric films 115 were, after the formation of ...
third embodiment
[0077]FIG. 8 is a vertical sectional view schematically showing the structure of the semiconductor laser device 3 of a third embodiment of the invention, and FIGS. 6 and 7 are vertical sectional views schematically showing its layer structure in the middle of its fabrication. The semiconductor laser device 3 of this embodiment is a modified version of the semiconductor laser device 1 of the first embodiment in which a dielectric film 118 is additionally formed inside the layered structure 101, in a portion thereof located right above the dislocation-concentrated region X1 of the n-type GaN substrate 100. In other respects, the n-type GaN substrate 100 is structured in the same manner as in the first embodiment.
[0078] The dielectric film 118 was formed in the middle of the formation of the ridge-formed structure. Specifically, after digging, as described earlier, the top surface of the p-type second contact layer 111 down to the middle of the p-type clad layer 109 by dry etching to ...
PUM
Property | Measurement | Unit |
---|---|---|
pitch | aaaaa | aaaaa |
width | aaaaa | aaaaa |
contrast | aaaaa | aaaaa |
Abstract
Description
Claims
Application Information
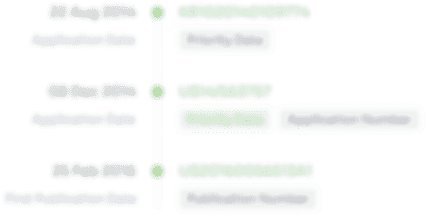
- R&D Engineer
- R&D Manager
- IP Professional
- Industry Leading Data Capabilities
- Powerful AI technology
- Patent DNA Extraction
Browse by: Latest US Patents, China's latest patents, Technical Efficacy Thesaurus, Application Domain, Technology Topic.
© 2024 PatSnap. All rights reserved.Legal|Privacy policy|Modern Slavery Act Transparency Statement|Sitemap