Manufacturing method for gas barrier film, and electronic member or optical member provided with gas barrier film
一种制造方法、阻气性的技术,应用在化学仪器和方法、液态化学镀覆、叠加层的镀覆等方向,能够解决增加工序数、不能获得阻气性能、生产率降低成本等问题,达到耐久性优异的效果
- Summary
- Abstract
- Description
- Claims
- Application Information
AI Technical Summary
Problems solved by technology
Method used
Examples
Embodiment 1)
[0132]On a cycloolefin copolymer film (manufactured by Polyplastics Co., Ltd., TOPAS 6017, thickness 100 μm, glass transition temperature 160° C., abbreviated as “COC” in Table 1.) as a substrate, coating containing A polymer compound solution (manufactured by Clariant Japan, AQUAMICA NL110-20) of perhydropolysilazane as a silicon-based polymer compound and xylene as a solvent so that the thickness after drying was 150 nm was applied to the obtained coating film. It was heated at 120° C. for 2 minutes to form a polymer compound layer.
[0133] It should be noted that when the cycloolefin copolymer film was immersed in xylene at 23° C. for 72 hours, the gel fraction of the cycloolefin copolymer film was 80%.
[0134] Next, argon (Ar) was plasma ion-implanted into the surface of the polymer compound layer under the following conditions by using a plasma ion implantation apparatus to fabricate a gas barrier film 1 in which a gas barrier layer was formed on a base material.
[01...
Embodiment 2~5)
[0146] In Example 1, except that the base material and the solvent shown in the following Table 1 were used as the base material and the solvent, it was carried out in the same manner as in Example 1, and Examples 2 to 2 in which a gas barrier layer was formed on the base material were produced. 5. Gas barrier films 2-5.
[0147] In addition, in Table 1, PC, PSF, and PVAC have the following meanings.
[0148] ・PC: Polycarbonate resin film (PUREACE, manufactured by Teijin Chemicals, thickness 100 μm, glass transition temperature 145°C)
[0149] ・PSF: polysulfone-based resin film (manufactured by BASF Corporation, ULTRASON S3010, thickness 55 μm, glass transition temperature 187°C)
[0150] • PVAC: polyvinyl acetal resin film (manufactured by Sekisui Chemical Industry Co., Ltd., SLEC KS-10, thickness 20 μm, glass transition temperature 110° C.).
PUM
Property | Measurement | Unit |
---|---|---|
gel fraction | aaaaa | aaaaa |
glass transition temperature | aaaaa | aaaaa |
gel fraction | aaaaa | aaaaa |
Abstract
Description
Claims
Application Information
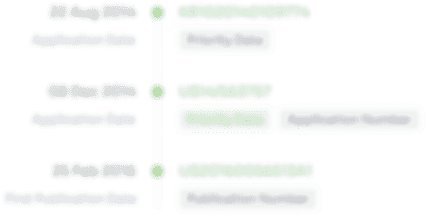
- R&D Engineer
- R&D Manager
- IP Professional
- Industry Leading Data Capabilities
- Powerful AI technology
- Patent DNA Extraction
Browse by: Latest US Patents, China's latest patents, Technical Efficacy Thesaurus, Application Domain, Technology Topic.
© 2024 PatSnap. All rights reserved.Legal|Privacy policy|Modern Slavery Act Transparency Statement|Sitemap