Burner
A burner and combustion chamber technology, applied in the direction of burner, combustion method, combustion type, etc., can solve the problems of increased emissions, flame front does not ensure uniform combustion, etc.
- Summary
- Abstract
- Description
- Claims
- Application Information
AI Technical Summary
Problems solved by technology
Method used
Examples
example 1
[0105] The combustion process is as Figure 1a According to the invention and connected to a burner of an industrial refractory boiler represented in . The burner is used at 100% of its thermal power (100% load). The fuel supplied is natural gas (about 95% methane, 2.5% ethane, 0.2% propane, 0.06% butane, 0.02% pentane + C 10 h 22 mixture, 1.6% nitrogen, 0.7% CO 2 、H 2 O trace and H 2 S). The oxidizer is atmospheric air at room temperature.
[0106] The air supply pressure is 12000 Pa. Gaseous fuel is supplied downstream of the injector 1 via an injection system 8 . The fuel supply pressure is 250000Pa.
[0107] Air excess is 1.5%. The oxygen contained in the flue gas is 0.3% by volume, calculated on a dry gas basis. The temperature of the flue gas output from the boiler was 1320°C.
[0108] The volume ratio of recycled flue gas / combustor is 45%. CO exhaust pipe emission ≤ 20 ppmv and NO x ≤15ppmv.
example 2
[0110] Example 1 was repeated, but the injection of natural gas was carried out upstream of injection section 1 via injection system 5 .
[0111] CO exhaust pipe emission ≤ 10 ppmv and NO x ≤10ppmv.
example 4
[0118] The combustion process takes place in a burner connected to an industrial boiler according to the invention. The burner is used at 100% of its thermal capacity. A fuel oil with a nitrogen content of 0.2% by weight was used. The combustor used is the same as in Example 1.
[0119] The air supply pressure is 12000 Pa. Fuel is supplied upstream of injection section 1 via injection system 5 . The fuel supply pressure is comprised between 10 and 15 bar (10000-15000 KPa). Air excess is 5%. The oxygen contained in the flue gas is 1% by volume of the dry gas. The temperature of the flue gas output from the boiler was 1250°C.
[0120] The volume ratio of recycled flue gas / combustor is 42%. Tailpipe emissions of CO are ≤40 ppmv and NO x ≤80ppmv.
PUM
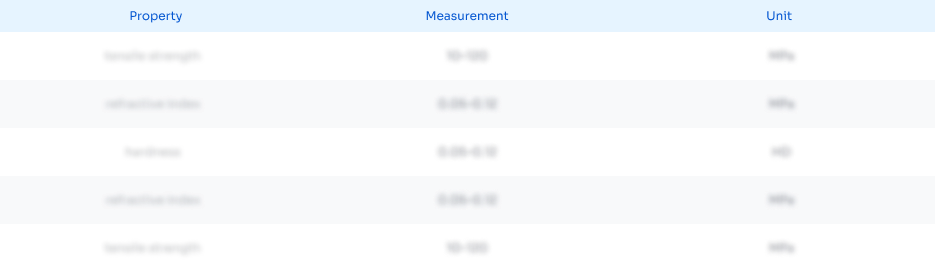
Abstract
Description
Claims
Application Information
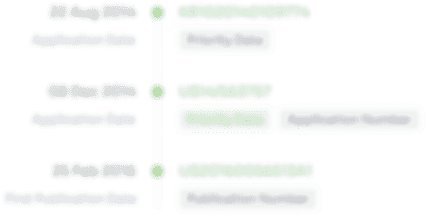
- R&D Engineer
- R&D Manager
- IP Professional
- Industry Leading Data Capabilities
- Powerful AI technology
- Patent DNA Extraction
Browse by: Latest US Patents, China's latest patents, Technical Efficacy Thesaurus, Application Domain, Technology Topic.
© 2024 PatSnap. All rights reserved.Legal|Privacy policy|Modern Slavery Act Transparency Statement|Sitemap