High-speed alloy steel for roller and preparation method of high-speed alloy steel
A technology of high-speed alloy steel and roll, applied in the field of high-speed alloy steel for roll and its preparation, can solve the problems of non-compliance, rework, waste of time and financial resources, etc., and achieve lower production cost, good wear resistance and corrosion resistance. strong effect
- Summary
- Abstract
- Description
- Claims
- Application Information
AI Technical Summary
Problems solved by technology
Method used
Examples
Embodiment 1
[0009] A high-speed alloy steel for rolls, which is composed of the following components: C: 2%; Si: 1.0%; Mn: 0.5%; Cr 5%; Mo: 2%; Ni: 1%; V: 0.2%; W: 0.2%; Nb: 0.05%; Ti: 0.15%; Al: 1%; P: 0.05%; S: 0.05%; Cu0.02%; Mg 0.15%; Al 2 o 3 1.5%; the balance is Fe, and the materials in the above ratio are added to the smelting furnace, and only 1.5%-3% of the initial C is added; Al 2 o 3 Only add 0.5%-1%; W does not add, P does not add, S does not add; After fully smelting in step 1, add the balance C, Al again 2 o 3、 W, P, and S are mixed evenly and added to the electric furnace for refining at one time. This step is very critical and also affects the performance of the roll; pour the refined molten steel into the mold to mold the roll to shape the roll; heat-treat the formed roll ; Grind the formed roll; check the performance of the roll, the roll after grinding meets the quality requirements, and deliver the product.
Embodiment 2
[0011] A high-speed alloy steel for rolls, which is composed of the following components: C: 2%; Si: 1.0%; Mn: 0.5%; Cr 5%; Mo: 2%; Ni: 1%; V: 0.2%; W: 0.2%; Nb: 0.05%; Ti: 0.15%; Al: 1%; P: 0.05%; S: 0.05%; Cu0.02%; Mg 0.15%; Al 2 o 3 1.5%; the balance is Fe, add the above-mentioned proportioned materials into the smelting furnace at one time, pour the refined molten steel into the mold and cast the mold to form the roll; heat-treat the formed roll; grind the formed roll ; Check the performance of the roll, the roll after grinding meets the quality requirements, and deliver the product.
Embodiment 3
[0013] A high-speed alloy steel for rolls, which is composed of the following components: C: 3%; Si: 1.5%; Mn: 0.5%; Cr 5%; Mo: 2%; Ni: 1%; V: 0.2%; W: 0.2%; Nb: 0.05%; Ti: 0.15%; Al: 1%; P: 0.05%; S: 0.05%; Cu0.02%; Mg 0.15%; Al 2 o 3 1.5%; the balance is Fe, and the materials in the above ratio are added to the smelting furnace, and only 1.5%-3% of the initial C is added; Al 2 o 3 Only add 0.5%-1%; W does not add, P does not add, S does not add; After fully smelting in step 1, add the balance C, Al again 2 o 3、 W, P, and S are mixed evenly and added to the electric furnace for refining at one time. This step is very critical and also affects the performance of the roll; pour the refined molten steel into the mold to mold the roll to shape the roll; heat-treat the formed roll ; Grind the formed roll; check the performance of the roll, the roll after grinding meets the quality requirements, and deliver the product.
[0014] Applicant the mechanical property of the alloy ...
PUM
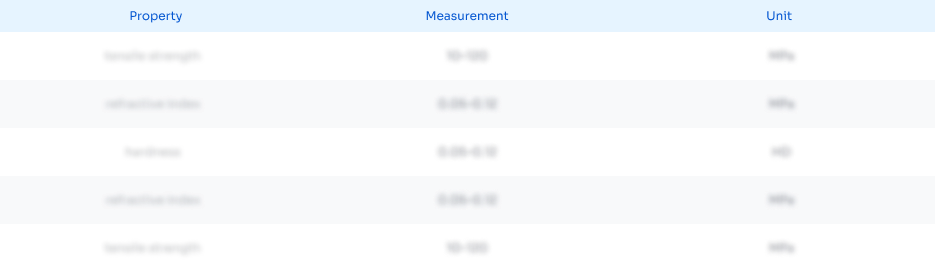
Abstract
Description
Claims
Application Information
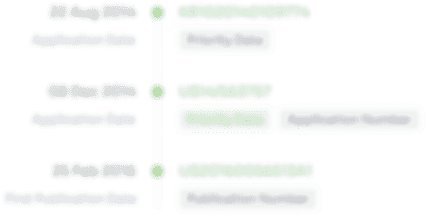
- R&D Engineer
- R&D Manager
- IP Professional
- Industry Leading Data Capabilities
- Powerful AI technology
- Patent DNA Extraction
Browse by: Latest US Patents, China's latest patents, Technical Efficacy Thesaurus, Application Domain, Technology Topic.
© 2024 PatSnap. All rights reserved.Legal|Privacy policy|Modern Slavery Act Transparency Statement|Sitemap