Anti-oxidation surface treatment method for conductive bar
一种表面处理、导电排的技术,应用在导电排生产,导电排抗氧化领域,能够解决要求高、处理方法不稳定、电镀行业污染大等问题,达到好附着的效果
- Summary
- Abstract
- Description
- Claims
- Application Information
AI Technical Summary
Problems solved by technology
Method used
Examples
Embodiment 1
[0023] The anti-oxidation surface treatment method of the copper conductive row described in this embodiment comprises the following steps:
[0024] Step 1: Surface cleaning, first configure the required cleaning solution, take phosphoric acid (85%), butoxyethanol, ethylene glycol lauryl ether, water and organic silicon as raw materials, the composition and quality of the cleaning solution The ratio is, phosphoric acid (85%): butoxyethanol: ethylene glycol lauryl ether: water: silicone = 9 parts: 5 parts: 6 parts: 70 parts: 0.5 parts The ratio is uniform, and the described The concentration of the cleaning solution is 8g / L, and the prepared cleaning solution is heated to 30°C. Soak the conductive row in the heated cleaning solution for 1 hour.
[0025] Step 2: After cleaning, take out the conductive row, rinse it with deionized water, and then wipe it with a trichlorethylene cotton cloth.
[0026] Step 3: configure soaking solvent, take formamide as solvent, mono-tert-butyl-...
Embodiment 2
[0029] This embodiment is basically the same as the method described in embodiment 1, except that the ratio of solvent and antioxidant is different in the third step.
[0030] Step 3 of this embodiment is: configure the soaking solvent, take formamide as the solvent, mono-tert-butyl-p-cresol as the antioxidant, and additionally take N,N-dibutyldithiocarbamate and aluminum formate for configuration , the above raw materials are configured according to the mass ratio, the formamide: mono-tert-butyl-p-cresol: formate: N,N-dibutyldithiocarbamate=22 parts: 6 parts: 4 parts : 0.5 parts: 0.2 parts, put the conductive discharge into the prepared organic solvent, slowly heat to 150°C, keep warm and pressurize at 150°C for 20h.
Embodiment 3
[0032] This embodiment is basically the same as the method described in embodiment 1, except that the ratio of solvent and antioxidant is different in the third step.
[0033] Step 3 of this embodiment is: configure the soaking solvent, take formamide as the solvent, mono-tert-butyl-p-cresol as the antioxidant, and additionally take N,N-dibutyldithiocarbamate and aluminum formate for configuration , the above raw materials are configured according to the mass ratio, the formamide: mono-tert-butyl p-cresol: formate: N,N-dibutyldithiocarbamate=25 parts: 8 parts: 4 parts : 0.5 parts: 0.2 parts, put the conductive discharge into the prepared organic solvent, slowly heat to 150°C, keep warm and pressurize at 150°C for 20h.
PUM
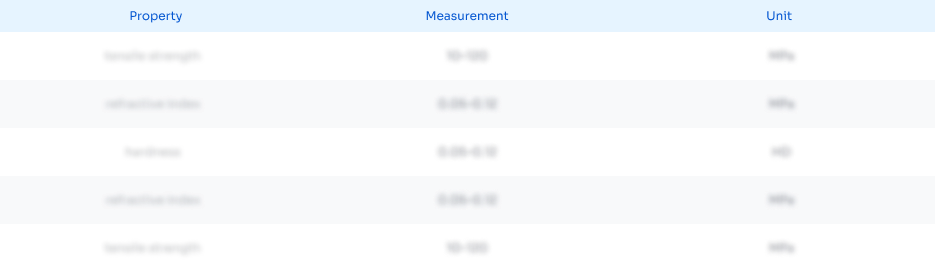
Abstract
Description
Claims
Application Information
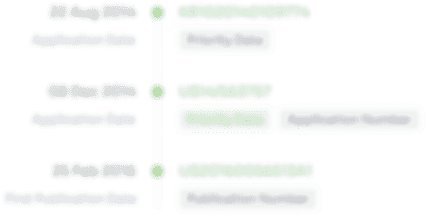
- R&D Engineer
- R&D Manager
- IP Professional
- Industry Leading Data Capabilities
- Powerful AI technology
- Patent DNA Extraction
Browse by: Latest US Patents, China's latest patents, Technical Efficacy Thesaurus, Application Domain, Technology Topic.
© 2024 PatSnap. All rights reserved.Legal|Privacy policy|Modern Slavery Act Transparency Statement|Sitemap