High-hardness and high-elasticity-modulus multi-component nitride coating and preparation method thereof
A high-elasticity, high-hardness technology, applied in the coating, metal material coating process, ion implantation plating, etc., can solve the coating performance, deposition conditions and deposition efficiency can not be balanced, performance requirements, can not meet high-speed cutting and Dry cutting and other problems, to achieve the effect of low cost, high elastic modulus, fast deposition speed
- Summary
- Abstract
- Description
- Claims
- Application Information
AI Technical Summary
Problems solved by technology
Method used
Examples
preparation example Construction
[0023] Preparation, characterization and measuring instruments used in the present invention:
[0024] JGP-450 Magnetron Sputtering System, Shenyang Scientific Instrument Development Center Co., Ltd., Chinese Academy of Sciences
[0025] D8 Advance X-ray diffractometer, Bruker, Germany
[0026] NANO Indenter G200 nanoindenter, Agilent Technologies, USA
[0027] Tecnai G 2 Model 20 high-resolution transmission electron microscope, FEI, USA
[0028] Quanta FEG450 scanning electron microscope (with Oxford energy spectrometer), American FEI company
Embodiment 1
[0030] A method for preparing a multi-component nitride coating with high hardness and high elastic modulus, comprising the steps of:
[0031] 1) A step of cleaning the substrate, cleaning the polished and mirror-polished substrate with 15-30kHz ultrasonic waves in alcohol and acetone for 10-15 minutes; then performing ion cleaning, during which the substrate is packed Into the sample chamber, vacuum to 5*10 -3 After Pa, open Ar gas, maintain the vacuum at 2-4Pa, use 13.56Hz (intermediate frequency) radio frequency to bombard the substrate with ions for 20-40min, and the power is 80-100W; the substrate is Cu.
[0032] 2) Using a multi-target magnetron sputtering apparatus, the step of magnetron sputtering reaction deposition is carried out on the substrate by an AlCrTiZrNb alloy target with an equal atomic molar ratio; the cleaned substrate is placed in a multi-target magnetron sputtering apparatus and left Before the AlCrTiZrNb alloy target material, the above-mentioned magn...
Embodiment 2
[0035] A method for preparing a multi-component nitride coating with high hardness and high elastic modulus, comprising the steps of:
[0036] 1) A step of cleaning the substrate, cleaning the polished and mirror-polished substrate with 15-30kHz ultrasonic waves in alcohol and acetone for 10-15 minutes; then performing ion cleaning, during which the substrate is packed Into the sample chamber, vacuum to 5*10 -3 After Pa, open Ar gas, maintain the vacuum degree at 2-4Pa, use 13.56Hz radio frequency to carry out ion bombardment on the substrate for 20-40min, and the power is 80-100W; the substrate is Al.
[0037] 2) Using a multi-target magnetron sputtering apparatus, the step of magnetron sputtering reaction deposition is carried out on the substrate by an AlCrTiZrNb alloy target with an equal atomic molar ratio; the cleaned substrate is placed in a multi-target magnetron sputtering apparatus and left Before the AlCrTiZrNb alloy target, the above-mentioned magnetron sputtering...
PUM
Property | Measurement | Unit |
---|---|---|
grain size | aaaaa | aaaaa |
coating thickness | aaaaa | aaaaa |
coating thickness | aaaaa | aaaaa |
Abstract
Description
Claims
Application Information
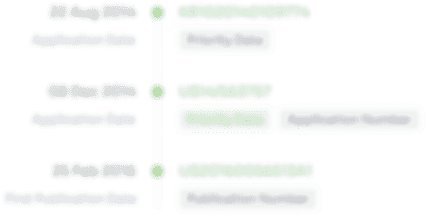
- R&D Engineer
- R&D Manager
- IP Professional
- Industry Leading Data Capabilities
- Powerful AI technology
- Patent DNA Extraction
Browse by: Latest US Patents, China's latest patents, Technical Efficacy Thesaurus, Application Domain, Technology Topic.
© 2024 PatSnap. All rights reserved.Legal|Privacy policy|Modern Slavery Act Transparency Statement|Sitemap