Method for improving epitaxial growth rate of silicon
A growth rate, silicon epitaxy technology, applied in crystal growth, single crystal growth, single crystal growth, etc., can solve the problems of silicon epitaxial surface growth quality degradation, aggravation of a large amount of adhesion reaction deposits, and silicon epitaxial wafer surface quality degradation. Achieve the effects of reducing process time and maintenance costs, significant technological breakthroughs, and improving production efficiency
- Summary
- Abstract
- Description
- Claims
- Application Information
AI Technical Summary
Problems solved by technology
Method used
Examples
Embodiment 1
[0036] (1) Raise the temperature of the base of the reaction chamber, set the temperature to 1180°C, inject hydrogen chloride gas to etch the reaction chamber, set the flow rate of hydrogen chloride gas to 18 L / min, and set the etching time to 230 sec
[0037] (2) The gaseous trichlorosilane carried by hydrogen was introduced as the growth raw material, the flow rate of hydrogen gas was set to 95 L / min, and the flow rate of gaseous trichlorosilane was set to 14 L / min. On the base of the reaction chamber Deposit the polysilicon cladding layer, and the deposition time is set to 20 sec.
[0038] (3) Purging the reaction chamber with hydrogen gas at a flow rate of 95 L / min, the purging time is set to 30 sec, and the reaction by-products are removed from the reaction chamber, and then the temperature of the reaction chamber is lowered to 200°C;
[0039] (4) Install the silicon substrate on the base of the reaction chamber, and raise the temperature of the base to 1125°C;
[0040] (...
Embodiment 2
[0046] (1) Raise the temperature of the base of the reaction chamber, set the temperature to 1160°C, inject hydrogen chloride gas to etch the reaction chamber, set the flow rate of hydrogen chloride gas to 19 L / min, and set the etching time to 230 sec
[0047] (2) The gaseous trichlorosilane carried by hydrogen was introduced as the growth raw material, the flow rate of hydrogen gas was set to 90 L / min, and the flow rate of gaseous trichlorosilane was set to 14 L / min. On the base of the reaction chamber Deposit the polysilicon cladding layer, and the deposition time is set to 30 sec.
[0048] (3) Purging the reaction chamber with hydrogen gas at a flow rate of 95 L / min, the purging time is set to 25 sec, and the reaction by-products are removed from the reaction chamber, and then the temperature of the reaction chamber is lowered to 200°C;
[0049] (4) Install the silicon substrate on the base of the reaction chamber, and raise the temperature of the base to 1120°C;
[0050]...
Embodiment 3
[0056] (1) Raise the temperature of the base of the reaction chamber, set the temperature to 1170°C, inject hydrogen chloride gas to etch the reaction chamber, set the flow rate of hydrogen chloride gas to 20 L / min, and set the etching time to 220 sec
[0057] (2) The gaseous trichlorosilane carried by hydrogen was introduced as the growth raw material, the flow rate of hydrogen gas was set to 95 L / min, and the flow rate of gaseous trichlorosilane was set to 16 L / min. On the base of the reaction chamber Deposit the polysilicon cladding layer, and the deposition time is set to 40 sec.
[0058] (3) Purging the reaction chamber with hydrogen gas at a flow rate of 90 L / min, the purging time is set to 30 sec, and the reaction by-products are removed from the reaction chamber, and then the temperature of the reaction chamber is lowered to 200°C;
[0059] (4) Install the silicon substrate on the base of the reaction chamber, and raise the temperature of the base to 1130°C;
[0060]...
PUM
Property | Measurement | Unit |
---|---|---|
diameter | aaaaa | aaaaa |
Abstract
Description
Claims
Application Information
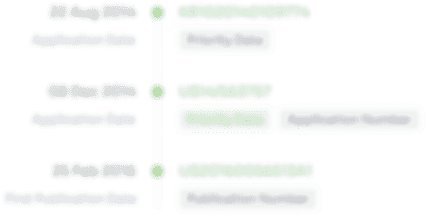
- R&D Engineer
- R&D Manager
- IP Professional
- Industry Leading Data Capabilities
- Powerful AI technology
- Patent DNA Extraction
Browse by: Latest US Patents, China's latest patents, Technical Efficacy Thesaurus, Application Domain, Technology Topic.
© 2024 PatSnap. All rights reserved.Legal|Privacy policy|Modern Slavery Act Transparency Statement|Sitemap