Method for metallizing ceramic surface and method for connecting ceramic with aluminum
a technology of surface metallization and ceramics, applied in metal-working apparatus, metallic material coating process, record information storage, etc., can solve the problems of difficult bonding between ceramics and aluminum, oxidation of aluminum cannot be avoided, rather bad or fluctuation of mechanical properties of bonding, etc., to increase the evaporation of aluminum.
- Summary
- Abstract
- Description
- Claims
- Application Information
AI Technical Summary
Benefits of technology
Problems solved by technology
Method used
Examples
example 1
[0106]The ceramic-surface-metallization apparatus mentioned above was adopted. Pure aluminum (99.9% ) was charged into the graphite crucible and alumina ceramic plates (137 mm in length, 35 mm in width, 0.64 mm in thickness, produced by Tsinghua Yueke Com, the purity is greater than 95% ) was inserted into the graphite guide traversed through the crucible. Aluminum was heated in a nitrogen atmosphere (the nitrogen flow rate is 20 Liters / min) to melt down and then was heated to 730° C. Another alumina plate was inserted into the guide from the entrance of the guide at the bottom of the apparatus at a speed of 68.5 mm / min, to push the ceramic plates inserted in the guide previously to move vertically at the same speed. During the moving, the ceramic plates contacted with aluminum melt in the crucible through the windows on the guide and then they were pushed out from the upper of the guide together with the aluminum melt adhered on the surface. After cooling, a layer of dense aluminum...
example 2
[0109]The experimental conditions were just the same as experiment 1 except that the temperature of the melt was decreased to 700° C. A dense aluminum film with an average thickness of 7 μm formed on the surface of the ceramic. The peeling off rate of the adhesive tape test was 0. The experiment was repeated three times and the results were same.
example 3
[0110]The experimental conditions were just the same as experiment 1 except that the temperature of the melt was raised to 760° C. A dense aluminum film with an average thickness of 5 μm formed on the surface of the ceramic. The peeling off rate of the adhesive tape test was 0. The experiment was repeated three times and the results were same.
PUM
Property | Measurement | Unit |
---|---|---|
temperature | aaaaa | aaaaa |
temperature | aaaaa | aaaaa |
equilibrium partial pressure | aaaaa | aaaaa |
Abstract
Description
Claims
Application Information
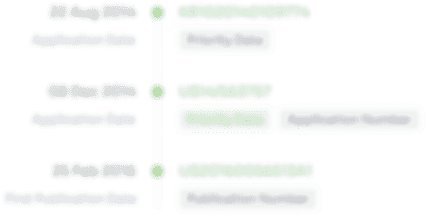
- R&D Engineer
- R&D Manager
- IP Professional
- Industry Leading Data Capabilities
- Powerful AI technology
- Patent DNA Extraction
Browse by: Latest US Patents, China's latest patents, Technical Efficacy Thesaurus, Application Domain, Technology Topic.
© 2024 PatSnap. All rights reserved.Legal|Privacy policy|Modern Slavery Act Transparency Statement|Sitemap