Zirconia-based all-ceramic false tooth and preparation method thereof
A zirconia-based denture technology, applied in the field of material science, can solve problems such as dullness, poor permeability, and prone to porcelain collapse, and achieve the effect of improving the overall mechanical properties, high bending strength, and good biocompatibility
- Summary
- Abstract
- Description
- Claims
- Application Information
AI Technical Summary
Problems solved by technology
Method used
Examples
Embodiment 1
[0016] Weigh 90 parts of ZrO according to mass ratio 2 , 9 copies of Y 2 o 3 , 0.5 parts of Al 2 o 3 , 0.01 parts of Fe 2 o 3 , 0.49 Er 2 o 3 Mix, then put into the mold and dry press at 20 MPa; vacuum-pack the molded product with a plastic bag, and then carry out isostatic pressing at 300 MPa; put the isostatically pressed product into a sintering furnace, The temperature is raised from room temperature to 1100° C. for 2 hours for pre-sintering to obtain a zirconia-based porcelain block.
[0017] Weigh 24.5 parts of CaCO according to mass ratio 3 , 50 parts of SiO 2 , 25 parts of MgO, 0.49 parts of Fe 2 o 3 , 0.01 Er 2 o 3 The powder was added with deionized water and mixed with zirconia mill for 24 hours, then dried at 120°C for 4 hours, and then calcined at 1100°C for 4 hours to obtain calcium magnesium silicon ceramic powder. To the above-mentioned calcium magnesium silicon ceramic powder, add 0.2 parts of fatty alcohol polyoxyethylene ether as a dispersant, ...
Embodiment 2
[0021] Weigh 94 parts of ZrO according to mass ratio 2 , 5 copies of Y 2 o 3 , 0.29 parts of Al 2 o 3 , 0.5 parts of Fe 2 o 3 , 0.01 Er 2 o 3 , 0.2 parts of MnO 2 Mix, then put into the mold and dry press at 3 MPa; vacuum-pack the molded product with a plastic bag, and then carry out isostatic pressing at 150 MPa; put the isostatically pressed product into a sintering furnace , from room temperature to 950 ° C for 4 hours for pre-sintering to obtain zirconia-based ceramic block.
[0022] Weigh 49.5 parts of CaCO according to mass ratio 3 , 49.3 parts of SiO2 , 0.5 parts of Fe 2 o 3 , 0.5 parts of Er 2 o 3 , 0.2 parts of MnO 2 The powder was added with deionized water and mixed with a zirconia mill for 4 hours, then dried at 80°C for 24 hours, and then calcined at 1250°C for 2 hours to obtain a calcium-magnesium-silicon ceramic powder. Add 0.1 part of methylcellulose as a binder to the above-mentioned calcium magnesium silicon ceramic powder, add 50 parts of deio...
Embodiment 3
[0026] Weigh 93.1 parts of ZrO according to mass ratio 2 , 6 copies of Y 2 o 3 , 0.1 parts of Al 2 o 3 , 0.2 parts of Fe 2 o 3 , 0.5 parts of Er 2 o 3 , 0.1 part of MnO 2 Mix, then put into the mold and dry press at 10 MPa; vacuum-pack the formed product with a plastic bag, and then carry out isostatic pressing at 250 MPa; put the isostatically pressed product into a sintering furnace , from room temperature to 1050 ° C for 3 hours for pre-sintering to obtain zirconia-based ceramic blocks.
[0027] Weigh 44.7 parts of CaCO according to mass ratio 3 , 45 parts of SiO 2 , 10 parts MgO, 0.01 parts Fe 2 o 3 , 0.19 Er 2 o 3 , 0.1 part of MnO 2 The powder was added with deionized water and mixed with a zirconia mill for 12 hours, then dried at 100°C for 8 hours, and then calcined at 1200°C for 2 hours to obtain a calcium-magnesium-silicon ceramic powder. To the above-mentioned calcium magnesium silicon ceramic powder, add 0.1 part of silicone resin as a dispersant, a...
PUM
Property | Measurement | Unit |
---|---|---|
Average bending strength | aaaaa | aaaaa |
Average bending strength | aaaaa | aaaaa |
Average bending strength | aaaaa | aaaaa |
Abstract
Description
Claims
Application Information
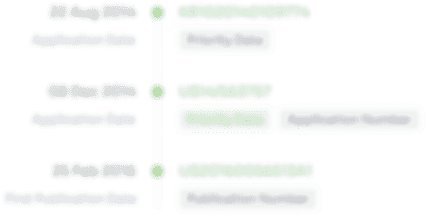
- R&D Engineer
- R&D Manager
- IP Professional
- Industry Leading Data Capabilities
- Powerful AI technology
- Patent DNA Extraction
Browse by: Latest US Patents, China's latest patents, Technical Efficacy Thesaurus, Application Domain, Technology Topic.
© 2024 PatSnap. All rights reserved.Legal|Privacy policy|Modern Slavery Act Transparency Statement|Sitemap